Marine Energy Manufacturing
NREL research and development capabilities are working to advance marine energy technologies by improving manufacturing processes and materials.
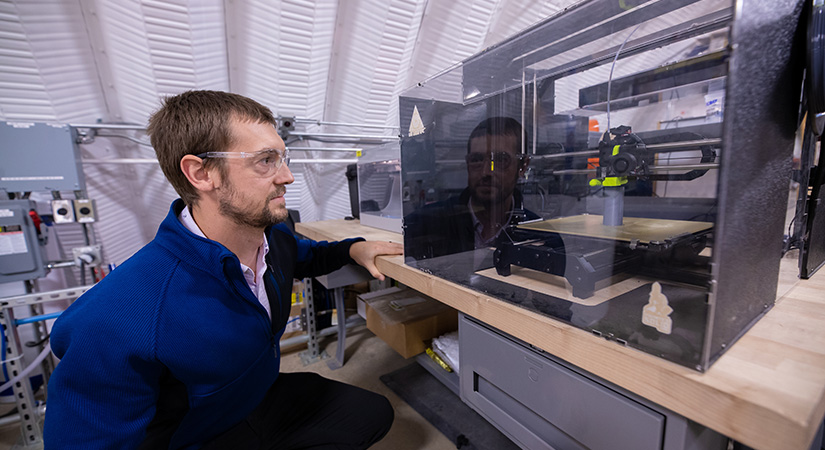
To achieve commercial success, marine energy technologies must be more cost-competitive and reliable to compete with other energy sources. NREL is working to advance marine energy composite materials, leading to more lightweight, high-quality materials that are also resilient to the harsh ocean environment.
Capabilities
Advanced Materials for Marine Energy Composites
NREL researchers worked with Verdant Power to construct turbine blades using thermoplastic composite materials. The new blades were deployed on one of Verdant Power's tidal turbines in New York City's East River for validation.
The NREL team has also developed and validated a novel recyclable bio-derivable epoxy that they are implementing into tidal turbine blades for further scale up and validation.
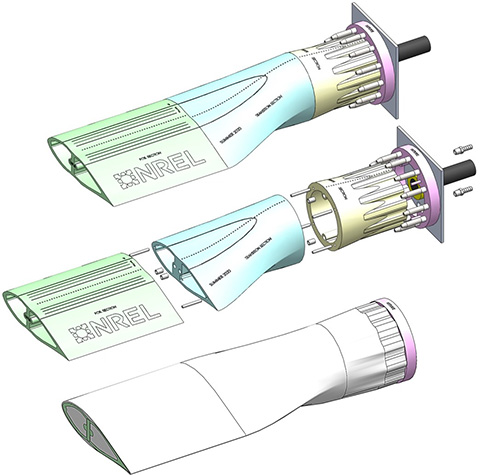
Rapid Prototyping
Marine energy system developers have a pressing need for more efficient and cost-effective prototyping techniques. To fill this innovation gap, NREL and Montana State University are exploring the potential for rapid prototyping using additively manufactured composite molds. With funding from the U.S. Department of Energy Water Power Technologies Office's Water Power Laboratory Seedling Program, NREL researchers have been pursuing a year-long effort to combine additive and composite manufacturing techniques into a faster, cheaper, and more repeatable process.
Working alongside Tennessee-based integrator One Off Robotics, NREL will develop and commission a Meltio-directed energy deposition machine, which can manufacture high-strength metal parts more than 1 meter tall. This additive manufacturing process is capable of printing near-net-shape structural parts out of metals like steel, stainless steel, titanium, and nickel alloys. With this new capability, NREL’s water power researchers are able to rapidly prototype high-strength components, such as tidal turbine blades and wave energy converter components.
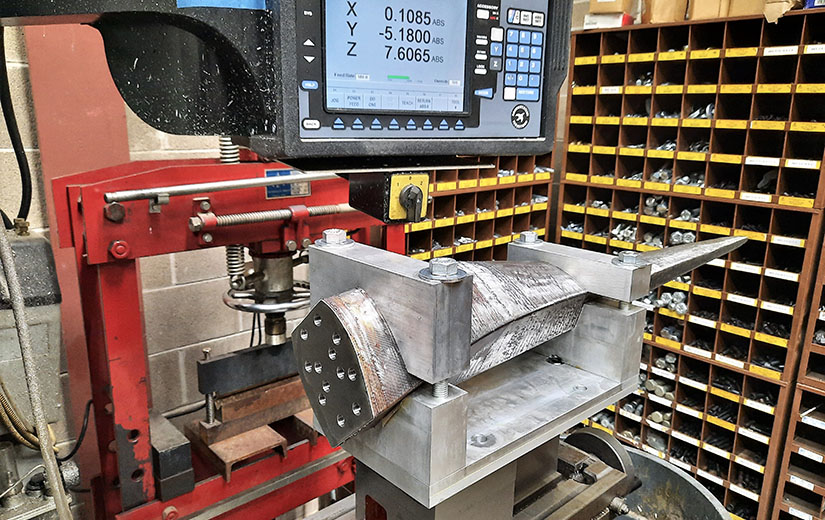
NREL also has a large plastic extruding system, developed in collaboration with California-based Orbital Composites, which employs the fused deposition modeling additive manufacturing method to create large parts out of high-strength plastics, such as nylon and acrylonitrile butadiene styrene. This system is mounted to the industrial robot research platform in NREL’s Composites Manufacturing Education and Technology Facility and has a working volume of approximately 6.6 by 2.5 by 2.5 meters. This system can be leveraged to rapidly prototype large plastic components for marine energy applications, such as nacelles, ballast, and floats.
Structural Validation Capabilities
Researchers perform full-scale structural validation on thermoplastic blades for tidal turbines at NREL's structural validation laboratories.
Publications
Investigating Marine Environmental Degradation of Additive Manufacturing Materials
for Renewable Energy Applications, Composites and Advanced Materials Expo (2023)
Subcomponent Validation of Composite Joints for the Marine Energy Advanced Materials Project, NREL Technical Report (2023)
Toward the Instrumentation and Data Acquisition of a Tidal Turbine in Real Site Conditions, NREL Technical Report (2023)
Leveraging the Advantages of Additive Manufacturing to Produce Advanced Hybrid Composite Structures for Marine Energy Systems, Applied Sciences (2021)
Structural Validation of a Thermoplastic Composite Wind Turbine Blade With Comparison to a Thermoset Composite Blade, Renewable Energy (2020)
Partner With Us
NREL offers a variety of ways for organizations to gain access to NREL's research expertise in marine energy technologies:
Partner with us through technology partnership agreements
Participate in subcontracted wind research through solicitations and requests for proposals
Use our cutting-edge research facilities to develop, validate, and evaluate wind technologies.
Contact
Share
Last Updated Dec. 31, 2024