Advanced Thermoplastic Resins for Manufacturing Wind Turbine Blades
The R&D 100 Award-winning thermoplastic resin system technology was developed with partner Arkema Inc. at the Composites Manufacturing Education and Technology (CoMET) Facility.
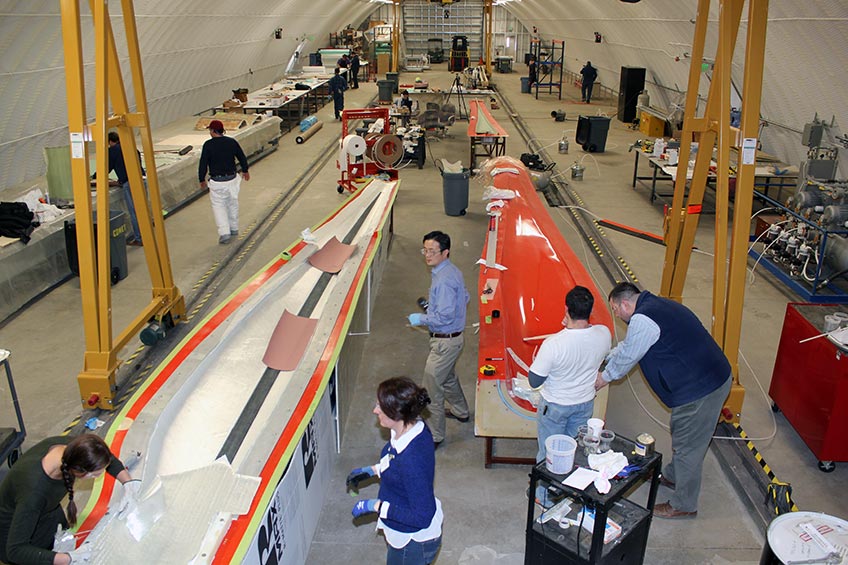
The vast majority of wind turbine blades in the United States ultimately end up in landfills at the end of their life, posing both environmental challenges and financial losses because of the lack of recovery of materials. And as wind energy continues to expand, so, too, will the pile of decommissioned blades left in its wake.
A truly sustainable, cost-effective, renewable energy revolution is now within reach, thanks to NREL's groundbreaking thermoplastic resin research for wind turbine blades. Our extraordinary technology will disrupt the wind energy industry's turbine manufacturing process, potentially enabling recyclable blades that no longer end their usefulness in a landfill.
Thermoplastic resins, combined with thermal welding techniques pioneered by NREL and partners, offer the potential for stronger, less expensive, and longer wind turbine blades, increasing energy capture, decreasing energy and transportation costs, and increasing blade reliability—critical to advancing the wind energy market.
These saltwater-safe thermoplastic blades also prime the marine energy industry for success, providing this emerging field with the durable, cost-effective materials on which to set sail.
Evolving Business-As-Usual Blades
Tapping into a wealth of fundamental wind energy science research, development, and validation activities and collaborations with industry partners, such as General Electric and TPI Composites Inc, NREL and Arkema Inc. have developed a game-changing, disruptive innovation to resolve tomorrow's wind industry challenges—the thermoplastic resin system for wind turbine blades.
Thermoplastics have the potential to revolutionize the wind energy industry, introducing a new era of next-generation materials, fabrication, testing, and welding techniques. Arkema's Elium resin is a two-part liquid reactive thermoplastic that blends together the advantages of thermoset and thermoplastic resins.
No Need for New Tools or Manufacturing Equipment.
Elium thermoplastic resins can serve as a drop-in replacement for epoxy.
No More Blade Burials.
Thermoplastics and thermal welding make recycling a snap.
Endurance Champion.
Improved structural dampening of thermoplastic blades leads to improved fatigue performance and turbine longevity.
Manufacturing Outcomes: Building the Blades
Until just a few years ago, there had only been small-scale demonstrations of this exciting, new material. Our team quantified and demonstrated how thermoplastic blades developed with Arkema's Elium thermoplastic resin, in conjunction with thermal welding, can be potentially recycled at their end of life, reducing the time, cost, and energy involved in manufacturing.
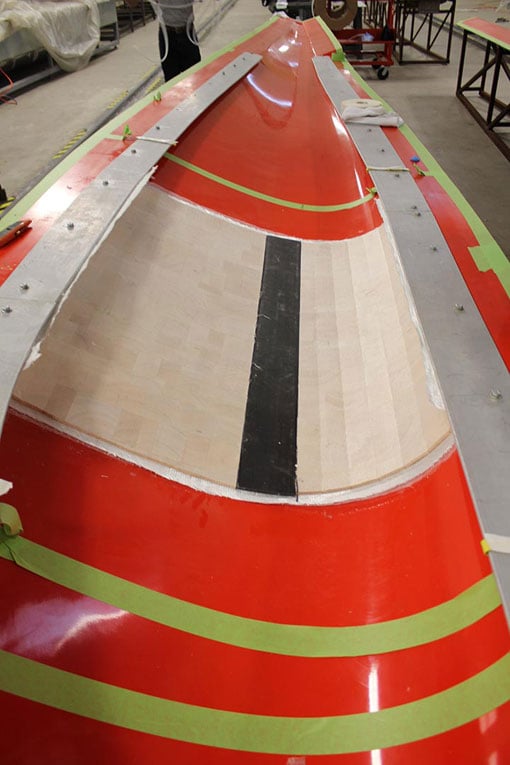
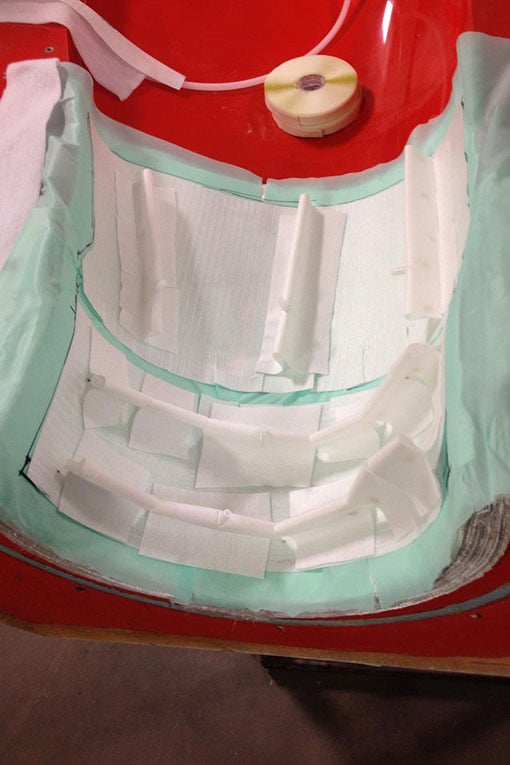
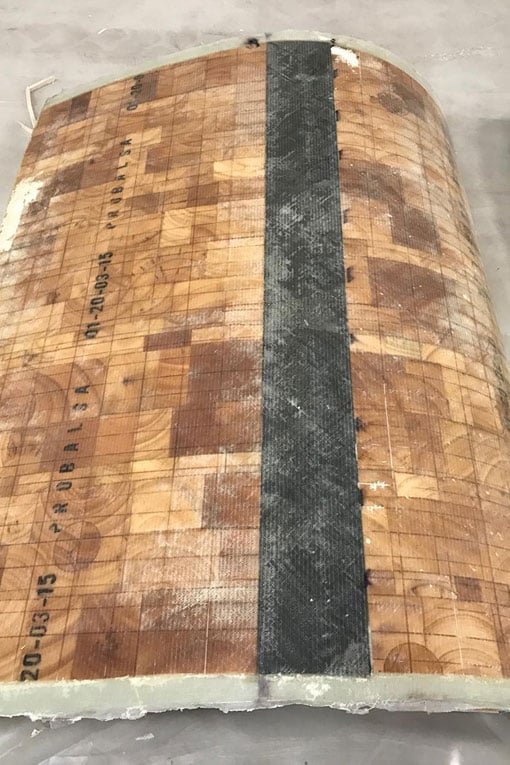
Photos of blade section manufacturing: balsa core and spar cap (left), second layer of fiberglass and flow media (center), and the finished product (right). Photos by Ryan Beach, NREL
To test this groundbreaking thermoplastic system, NREL researchers first constructed a 9-m turbine blade to demonstrate manufacturability and then a 13-m blade that they put to the test, validating the blade for strength and other performance characteristics.
The 9-m wind blade, produced at NREL's CoMET facility, exhibited impressive results, such as reduced equipment costs and cycle time.
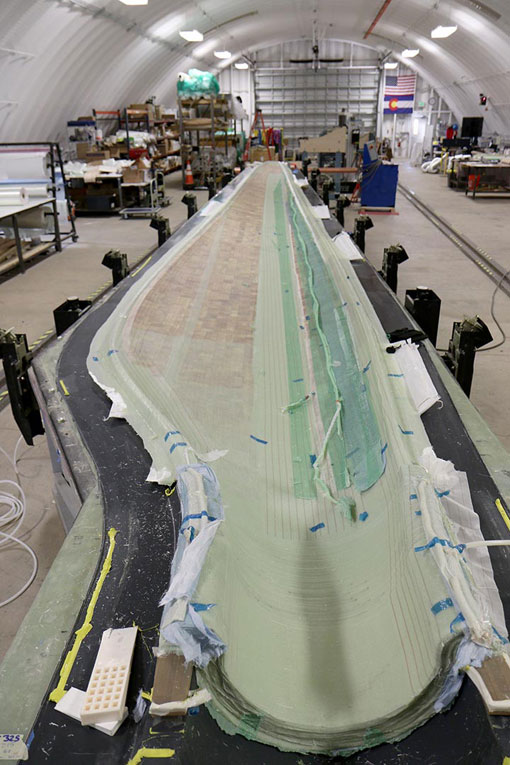
Building a 13-m thermoplastic blade at NREL's CoMET facility. Photo by Ryan Beach, NREL
The team then built a 13-m blade, employing the cutting-edge structural validation laboratories at the Flatirons Campus to test it.
It found that the thermoplastic blade had similar stiffness to an epoxy blade. It simulated 20 years of use on the blade to evaluate durability. The Elium thermoplastic blade exhibited five to seven times higher levels of structural damping than the epoxy blade. These findings suggest that by employing thermoplastic blades, we can also expand the life span of the entire turbine.
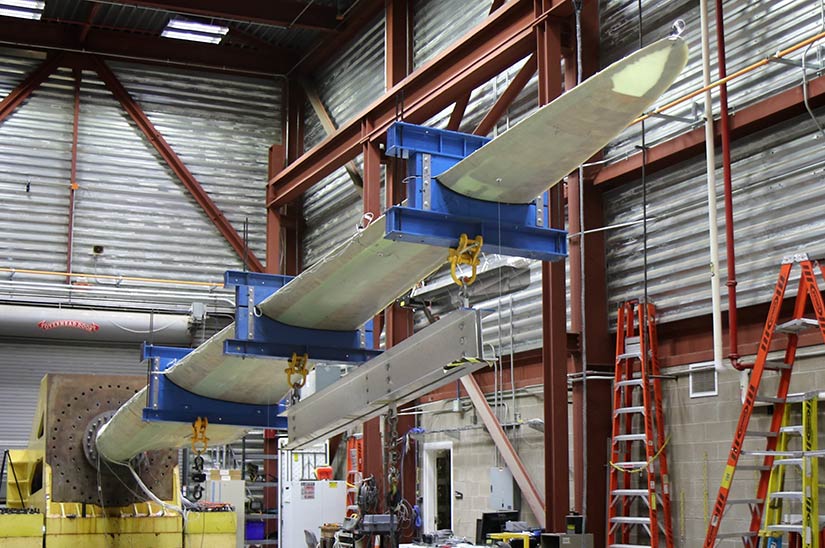
In it for the long haul: NREL simulated 20 years of use of the thermoplastic blade to ensure durability. Photo by Ryan Beach, NREL
Impact
These next-generation thermoplastic blades build off the successes of the business-as-usual epoxy blades and transform them into an environmentally friendly, cost-effective blade of the future. The researchers found that the process and material demonstrated potential for:
- Recyclability: The Elium thermoplastic blades exhibit the potential to be recycled, reducing both landfill waste and disposal costs.
- Thermal welding: Materials can be thermally joined, enabling the manufacture of potentially stronger and lighter blades.
- On-site manufacturing: Blades can be built on-site, allowing for the development of larger blades at greatly reduced transportation costs.
- Ease of repair: Unlike epoxy blades that necessitate traditional grinding repairs, thermoplastics can be reheated at just the point of repair and reshaped.
- Marine energy applications: Thermoplastic material performs better than traditional materials in seawater, making this material a game changer for marine energy applications.
- Reducing the equipment capital costs associated with blade production by up to 30%
- Decreasing the critical cycle time during production by up to 20%.
NREL's thermal welding technique—coupled with Arkema's resin system—earned a 2020 Special Recognition Award from R&D 100 for being a "market disrupting" technology. Watch the video to learn more about this game-changing wind and waterpower innovation.
Capabilities
Composites Manufacturing
The CoMET Facility provides a wide range of capabilities, including:
- Rapid prototyping of new blade materials and production methods
- Full-scale blade component tooling and fixtures (root, spar cap, tip, shear web)
- Infusion, pultrusion, prepreg, RTM, hand lay-up (small parts)
- Polyester, vinyl-Ester, epoxy, thermoplastic/fiberglass, carbon fiber
- Comprehensive composite production equipment (mixers, vacuum, dispensers)
- Molding, assembly, bonding, and finishing
- Thermal welding
- Segmented 3-D printed tooling
- Large-area rapid nondestructive evaluation
- Modeling and manufacturing simulation
- Panels, material test coupons, and components
- Structural evaluation of coupons, components, and joints
- Industrial robotic platform for automation research
- Composite recycling processing and material characterization
- Workforce development and training for the composites industry.
Learn more about the CoMET Facility and its many capabilities.
Structural Validation Capabilities
Researchers perform full-scale structural validation on the thermoplastic blades at NREL's structural validation laboratories.
Publications
Structural Validation of a Thermoplastic Composite Wind Turbine Blade With Comparison to a Thermoset Composite Blade, Renewable Energy (2021)
Fusion Joining of Thermoplastic Composite Wind Turbine Blades: Lap-Shear Bond Characterization, Renewable Energy (2019)
Recycling Glass Fiber Thermoplastic Composites from Wind Turbine Blades, Journal of Cleaner Production (2019)
Techno-Economic Analysis of a Megawatt-Scale Thermoplastic Resin Wind Turbine Blade, Renewable Energy (2019)
Manufacturing and Flexural Characterization of Infusion-Reacted Thermoplastic Wind Turbine Blade Subcomponents, Applied Composite Materials (2019)
Innovative and Recyclable Thermoplastic Wind Turbine Blades, NREL Fact Sheet (2019)
Manufacturing a 9-Meter Thermoplastic Composite Wind Turbine Blade, American Society for Composites 32nd Technical Conference (2018)
Partners
NREL partners with industry, academia, and national laboratories. An industrial-scale workspace designed to welcome workforces and technologies across the composites materials industry, the CoMET Facility is equipped to support such large-scale collaborative efforts.
Contact
Share
Last Updated Jan. 13, 2025