Advanced Manufacturing and Materials
NREL's collaborative research environment enables scientists to push wind energy industry frontiers in advanced manufacturing and materials.
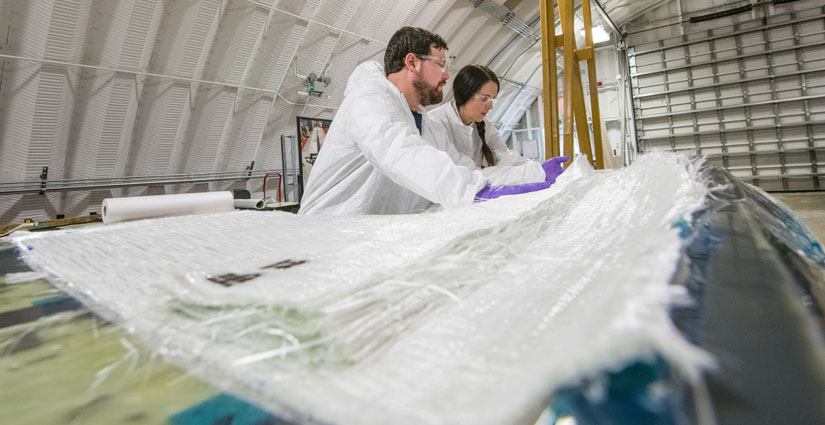
Novel wind turbine manufacturing processes have the potential to increase production capacity, product reliability, and recyclability, while reducing dependence on foreign supply chains, decreasing product costs, and overcoming barriers such as transportation of large-scale wind turbine blade structures. NREL's Advanced Manufacturing team works to realize these benefits through our Composites Manufacturing Education and Technology (CoMET) facility and Institute for Advanced Composites Manufacturing Innovation (IACMI) leadership.
Partner With Us
See a summary slide deck of NREL's wind-energy-related advanced manufacturing and materials capabilities, research, and projects. Explore more below.
Learn more about how to work with us.
Materials Research and Applications
NREL is at the forefront of research into thermoplastic resins, an advanced composite material that would make wind turbine blades more recyclable, while enabling longer, lighter-weight, and lower-cost blades. NREL is also accelerating the commercialization of additive manufacturing and next-generation technologies and processes such as new, low-cost, 3D-printable magnet materials.
Areas of Expertise
- Identify and develop advanced composite materials
- Provide information on quantity, uses, availability, and properties of wind energy materials
- Accelerate commercialization of additive manufacturing and next-generation technologies and processes
Manufacturing Processes at Scale
NREL performs foundational research into next-generation wind turbine manufacturing processes that will enable the factories of the future. In addition to techno-economic modeling and LCOE impact analyses, our experts have access to the equipment and materials that can transform design concepts into prototypes, and from prototypes to products.
Areas of Expertise
- 3D-printed, large-scale, composite blade structures and electromagnetic wind turbine generators
- Recyclable materials and thermoplastic resin systems
- Thermal welded/fusion-composite joining technologies
- Automated blade manufacturing processes
- Techno-economic modeling and LCOE impact analyses
Manufacturing Optimization, Onsite and Modular Manufacturing
NREL is researching how new and emerging Industry 4.0 technologies in material science, high-performance computing, automation, and 3D printing can impact large-scale wind turbine blade manufacturing to enable advanced manufacturing solutions. Our multipronged approach leads to lower costs as high stiffness-to-weight ratio and high strength-to-weight ratio sandwich composite structures enable onsite manufacturing and lighter blade structures.
Areas of Expertise
- Wind turbine market and techno-economic analyses
- Topology optimization, large-scale 3D printing, additive materials properties, and additive design guidelines
- High-tolerance, repeatable, low-cost production technologies suitable for onsite and modular manufacturing
Recycling and Reuse for a Circular Economy
NREL envisions a circular economy for wind energy materials that are designed to use fewer resources, last longer, and recycle more easily. Part of this work involves techno-economic analysis to understand the scope of the challenges and evaluate the economic and social considerations that could govern a circular economy.
NREL is also developing innovative recycling solutions for composite materials, including for both existing thermoset blade materials and future blade materials. For current-generation blades, NREL is exploring cost-effective means of recycling. For the next-generation of blades, NREL is developing two new approaches: thermoplastic resin blades that can be melted and recast at end-of-life and reversible, bio-based resins that allow for easier recycling.
Areas of Expertise
- Thermoplastic material system characterization and processing for wind turbine blades at scale
- Composite processing and structural validation
- Polymer chemistry for composite materials
- Modeling and analysis of circular economy opportunities, solutions, and transitions
- Wind turbine blade design and manufacturing processes and requirements
- Lifecycle assessment for structures and materials
- Industry collaborations across supply chains
Share
Last Updated May 22, 2025