Nine Reasons To Partner With NREL’s CoMET Facility
Learn How the CoMET Can Take Composite Materials From Theory to Market
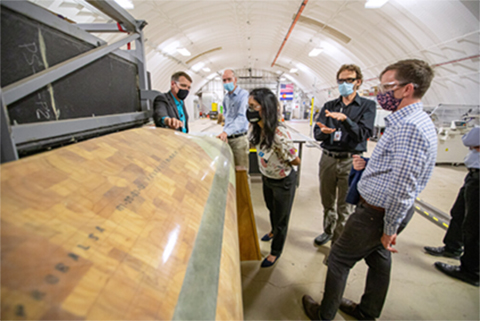
What do Kevlar vests, carbon-fiber airplane wings, and mud bricks have in common?
They are all composite materials—a happy merger of two or more ingredients that forge stronger, lighter-weight, cheaper, or more durable or flexible materials. They are everywhere—in bicycle frames, concrete sidewalks, car doors, wind turbine blades, surfboards, and much more.
Today, researchers are designing novel composite materials that can build stronger, more affordable, and even sustainable products. But, unlike the ancient Egyptians, who simply layered straw and silt to build their tough, mud bricks, modern manufacturers need far more complex equipment to take new composites from theory to prototype and, eventually, manufacture a commercial-scale product.
The National Renewable Energy Laboratory’s (NREL’s) Composites Manufacturing Education and Technology Facility—CoMET—is one of a handful of facilities in the United States with the specialized equipment and human expertise to do just that. Since its launch in 2016, the 10,000-square-foot facility hosted partnerships primarily with members of the wind energy industry to design stronger, lighter weight, less expensive, and even recyclable wind turbine blades. But the CoMET Facility’s capabilities reach beyond the wind energy industry; it can also help industry partners and university researchers discover specialized composite materials for marine energy turbines (which generate energy from rushing rivers and oceans), transportation, or sustainable, energy-efficient buildings.
“The CoMET has already played a critical role in advancing research in both the wind power and the water power industries,” said Derek Berry, a senior wind technology engineer at NREL. “But we can also play a critical role in developing new materials for car doors and airplane wings or building facades and insulation. Anywhere we can increase energy efficiency through new materials and composites or new manufacturing processes, we can have an impact.”
As a result of a funding partnership between the U.S. Department of Energy’s Advanced Manufacturing Office, the Institute for Advanced Composites Manufacturing Innovation, the state of Colorado, and NREL, the CoMET can help researchers design specialized materials or automate their manufacturing processes to make them more efficient, cost-effective, and safe.
“Composite material structures will be critical to help drive a renewable energy future and help reach our decarbonization targets,” said Matthew Ringer, the laboratory program manager for advanced manufacturing at NREL.
For October’s Manufacturing Month (and Manufacturing Day on October 1), here are nine ways the CoMET can help bring an idea from theory to market:
- Upscale a design. In the CoMET Facility, we can start small—with models and simulations—before rapidly scaling up composite materials into larger prototypes. As a bonus, we can haul completed commercial-scale structures across the street to stress-test the design in NREL's structural validation laboratories.
- Automate the manufacturing process—with robots. In a recent partnership between NREL and General Electric/LM Wind Power, a collaborative team invented a new, automated method for manufacturing bigger (and better) wind turbine blades. Bigger blades are more cost-effective and produce more energy, but their size makes them tricky to build. An automated manufacturing process can reduce the labor, cost, and time needed to produce these massive pieces. And, this year, the CoMET Facility added an industrial robotic platform to further research working to perfect automated manufacturing.
- Take advantage of another CoMET specialty—VARTM. NREL engineers are experts in vacuum-assisted resin transfer molding (VARTM), a cost-efficient method of combining and compressing composite materials into large, high-performance structures. This method can also make smaller, intricate parts that can withstand intense loads. For example, the smallest wind turbine components must survive the strongest winds to ensure a turbine can endure for decades.
- Weld a stronger future. Wind turbine blades can last longer with another CoMET Facility capability—thermal welding. Rather than fusing blade components with epoxy, NREL engineers use this novel welding technique to bind the blades better than any adhesive and prolong their life span.
- Reduce costs and waste. A recent partnership between NREL and Arkema Inc. resulted in an award-winning, new material for wind turbine blades: Elium thermoplastic resin. The composite material—which, to oversimplify a complex chemical process, softens when heated and hardens when cooled—is not only recyclable (unlike traditional epoxy blades) but is also more durable and cost-effective. The blades earned an R&D 100 Award and the moniker “market disrupter” for their revolutionary design and later proved their resilience in Verdant Power’s saltwater tidal energy turbines. The CoMET can help other partners conceive, characterize, and create similarly innovative materials.
- Stack up (or lay-up). Stacking materials in a mold—also known as lay-up manufacturing—can be time- and labor-intensive but produces highly complex composite structures arranged for optimal strength and durability. The CoMET has both the equipment and expert technicians necessary to perform this manual technique.
- 3D-print novel molds. In the CoMET Facility, partners can try out new materials or shapes for whole wind turbine blades or individual components (like the blade tip) to see what works best. Eventually, the CoMET could help wind manufacturers (and developers in marine energy, transportation, and energy-efficient buildings) plan how to manufacture their components on-site to reduce the costs and carbon emissions of transporting large components, like 70-meter wind turbine blades, across the country.
- Switch to bio-based resins to reduce carbon emissions. NREL engineers plan to explore using resins from plants, like corn, soybeans, or algae, to build wind turbine blades. This swap could help make the manufacturing process “greener” by reducing the need for petrochemicals.
- Develop a modern manufacturing workforce. NREL is committed to developing and training the next generation of composite manufacturers. Since 2017, the facility has hosted eight interns. CoMET experts trained five composite technicians to earn certification, co-hosted three workshops with Composites One that attracted about 150 attendees each, and, in February 2020, hosted a group of 34 women from the Women in Manufacturing Association’s Colorado Chapter. Once the COVID-19 pandemic slows enough to ensure in-person events are safe, CoMET researchers will resume their outreach to help inspire and grow the modern manufacturing workforce.
“As we expand into other research areas,” Berry said, “we'll have an opportunity to impact the factories of the future. Whether we're performing research on automation at scale, sustainability, or the circular economy, we'll help to enable U.S. manufacturing to be more competitive and more energy-efficient.”
Learn the many ways organizations can work with NREL’s CoMET Facility and expert team:
- Partner with us through technology partnership agreements.
- Participate in subcontracted wind research through solicitations and requests for proposals.
- Use our cutting-edge research facilities to develop, validate, and evaluate wind, water, and other technologies.
Last Updated May 28, 2025