Structural Validation Laboratories
NREL engineers design experiments and perform structural validation in structural test laboratories using representative forces and environmental conditions that recreate extreme in-water conditions.
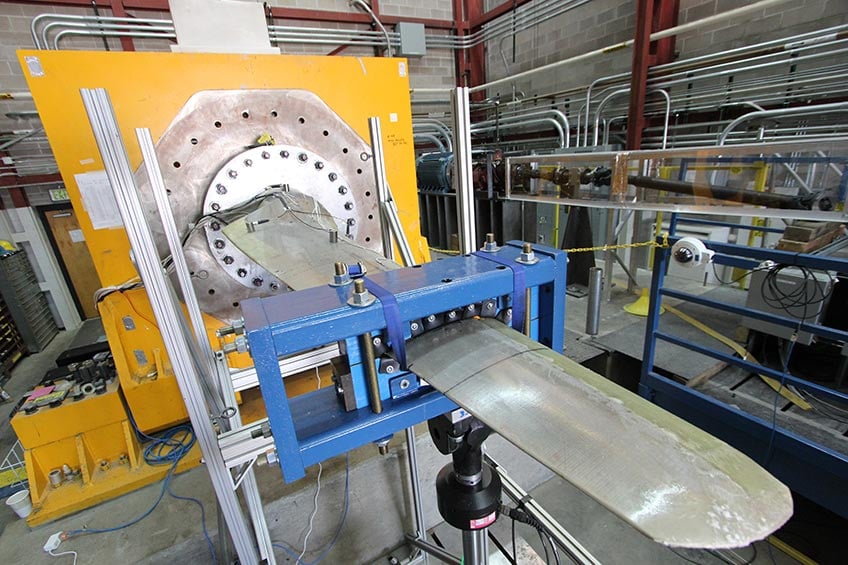
Component and full-scale structural validation of marine and hydrokinetic system mechanical components validate models, demonstrate system reliability, enable value engineering, and demonstrate structural and functional readiness for deployment.
Capabilities
NREL complements modeling and analysis capabilities with facilities and equipment needed for structural validation of marine and hydrokinetic devices. NREL's facilities and capabilities are uniquely suited for characterizing materials and performing structural validation of components and complete systems.
Property Validation
- Measure intrinsic structural properties, including mass, center of gravity, and moment of inertia for complex components and systems to ensure conformity with design specifications
Dynamic Characterization
- Provides designers with the natural frequencies, damping values, and mode shapes of components and systems
Static Strength Verification
- Validate structural properties of components and systems
- Characterize structural response from extreme load conditions, such as inflow direction changes, extreme flow conditions, and loss of grid connection
- Measure and quantify strength design margins by testing to failure
- Use multidirectional loading to create representative load conditions
Fatigue Durability Verification
- Simulate discrete dynamic events
- Conduct lifetime design validation through amplification and acceleration of service loads to shorten duration laboratory loading
- Verify as-manufactured properties at any stage of the product development cycle
- Perform extensive structural performance measurements using discrete and full-field strain, acoustic emission, ultrasonic, and thermographic techniques
- Evaluate nondestructive inspection technologies
Laboratory Facilities and Equipment
- A 70-meter long, 1,000 square-meter facility for test article preparation and composite material development
- Up to 1,800 square meters of laboratory space across three test facilities
- Reinforced laboratory structural floors
- Five validation stands with overturning moment capacities from 100 kilonewton-meters to 16.7 meganewton-meters
- A 100-kilonewton load frame for coupon and element testing
- A 500-kilonewton load frame for component validation
- Servo-hydraulic actuators with pistong displacements to 1.5 meters and force capacities up to 500 kilonewtons
- Servo-electric winches for quasi-static load application
- Extensive data acquisition and sensing capabilities for measuring structural properties
- Electric and fiber optic strain and measurement systems.
Read NREL's fact sheet on structural evaluation.
Share
Last Updated Feb. 17, 2025