Advancing Wide-Bandgap Power Modules
NREL's advanced modeling and experimental capabilities are being used by GE Aviation Systems, a subsidiary of General Electric (GE), to improve the thermal performance and reliability of its wide-bandgap power modules.
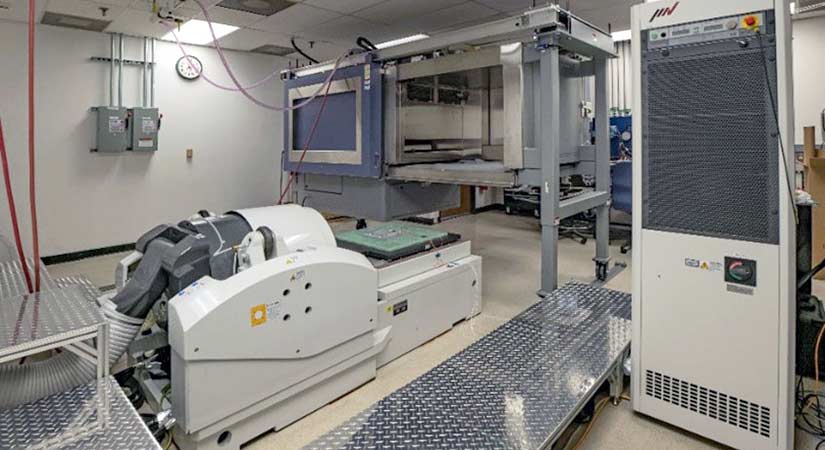
NREL's team works to overcome challenging technical barriers to the commercialization of electric-drive vehicles, aircraft, and other power electronics using high-temperature power module packaging based on silicon carbide and gallium nitride. Leveraging GE's more than 10 years of experience in wide-bandgap device development and high-density, high-temperature packaging of devices into modules, NREL provides solutions to performance and reliability gaps in wide-bandgap power electronics applications.
Impact
Wide-bandgap components incorporating devices made from silicon carbide and other advanced materials can give certain aviation and other power electronics systems a competitive advantage in the marketplace by:
- Reducing power electronics components size
- Reducing costs at the system or component level
- Improving efficiency and performance of the power electronics.
NREL's work with GE Aviation Systems provides advanced modeling and experimental evaluation capabilities and highlights the benefits of collaboration between industry and the national laboratories.
Capabilities
NREL's state-of-the-art capabilities offer a range of support to this project, including:
- Modeling, simulation, and computational analysis of module internal structures, interconnects, and thermal performance
- Experimental reliability verification and evaluation of the modules
- Insight and lessons learned from past power module experience to help inform the design phase of the project.
NREL's world-class facilities and equipment enable experimental and modeling capabilities for power electronics.
Thermal Management Modeling
Modeling the thermal (steady-state and transient) performance of the GE power module evaluates the effects of coolant temperature and convective cooling performance. Thermal analysis tools like computational fluid dynamics simulations are used to evaluate thermal performance, predict the thermal resistance versus flow rate characteristics, and gain insight into critical thermal contact resistances within the module assembly.
Thermomechanical Modeling
Modeling stress, strain, and strain energy density within the packaging stack-up helps understand the impact on reliability of the package/module.
Lifetime Prediction Models
To estimate the reliability and longevity of the GE power modules, NREL uses lifetime prediction models to compute predicted cycles-to-failure results for a particular failure mode.
Vibration Testing and Evaluation
Using NREL's electrodynamic shaker, vibration profiles were completed on four GE power modules—two under a sinusoidal profile and two under a mechanical shock profile. Results of the vibration profiles showed no degradation or failures, meaning the modules successfully withstood the accelerated conditions and are ready for implementation within multiple GE applications.
Contact
Share
Last Updated Jan. 13, 2025