Systems Engineering 2013 Workshop
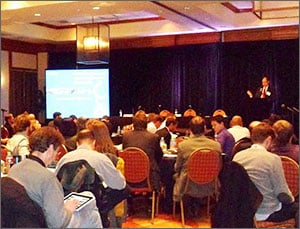
Paul Veers addresses the workshop attendees at the end of the second day of the workshop. Image from NREL
The 2nd NREL Wind Energy Systems Engineering Workshop took place on the 29th and 30th of January 2013. The workshop showcased research and development activities in the areas of systems engineering and techno-economic modeling of wind energy systems and provided opportunities for discussion about potential future developments and collaborations. Follow-on meetings on the 31st of January and 1st of February featured software tutorials and smaller group meetings for discussion.
Highlights included a variety of expert panel sessions on topics such as:
- Wind Energy System Costs from Turbines to Plants
- Systems Engineering Methods Applied to Wind Energy Research Design and Development
- Industry Perspectives on Systems Engineering Practices from Components to Projects
- Integrated Wind Turbine and Plant Modeling
- Wind Plant Design and Optimization
Meeting Agenda and Presentations
The full program including abstracts and biographical information on the authors is available. Links to PDF versions of many of the presentations are available in the summary of the meeting agenda below.
Poster session abstracts and biographical information on the presenters is available.
Tuesday — January 29, 2013
- Nick Johnson, Department of Energy
Systems Engineering Workshop — DOE's Perspective - Paul Veers, Ph.D. NREL National Wind Technology Center
Keynote Address: System Innovation in Wind Energy
Summary: The DOE program is committed to reducing the levelized cost of energy (LCOE) of wind systems through a program that both fosters innovation with technology development and enhances the speed of development through barrier removal. Nick Johnson provided an overview of the Wind and Water Power Program (WWPP) that is supporting the accelerated development of wind energy systems, with a new emphasis on the entire wind plant as the critical focus of advancement. The NREL Systems Engineering effort is sponsored by the DOE WWPP to foster their goals through the synthesis of individual technology innovations into the context of the plant LCOE. The importance of accurately reflecting the design requirements of each subsystem, and the interactions between subsystems, in the system engineering model was emphasized by Paul Veers. A subsystem example of a blade system design effort that introduced innovation through the integration of manufacturing requirements into the aerodynamic design of blades was used to illustrate the opportunity for systems engineering at a broader scale.
- Eric Lantz, NREL Strategic Energy and Analysis Center
Understanding Wind Power Costs: The Value of a Comprehensive Approach - Ir. Bernard Bulder, ECN, the Netherlands
Integrated Wind Farm Design and Optimization - Rajan Arora, RES Americas
Impact of Project Financing on Wind System Design
Summary: There are many project planning aspects that need to be accounted for to optimize wind energy competitiveness. Operation and maintenance costs are substantial and great care should be taken in planning for operational expenses. To do so, one must understand the impacts of losses and induced loading from wakes. One possible solution to this may be the introduction of wind plant controls. The lenders look very closely at design aspects of the project with a special emphasis on turbine technology which means all of these system level analyses must be conducted before a project can even be financed. While evaluating the turbine, they look at items such as the deployment history of the turbine, any known turbine issues, the suitability of the turbine for the specific project site, and any known serial defect issues. The bottom line indicates that a single focus optimization will certainly lead to a non-optimal system design. In order to get to the optimum system design, all aspects of the project must be planned and optimized as a single integrated system.
- Carlo Bottasso, Ph.D. Politecnico di Milano, Italy
Multidisciplinary Design Optimization of Wind Energy Systems - Andrew Ning, Ph.D. NREL National Wind Technology Center
Objectives and Constraints for Wind Turbine Optimization - Ryan Schkoda, Ph.D. Clemson Wind Turbine Drivetrain Testing Facility
Systems Engineering Activities at Clemson University's International Center for Automotive Research (CU-ICAR) and Wind Turbine Drivetrain Testing Facility
Summary: As wind power matures, and offshore applications become more accessible, there is a fundamental need to reduce costs across the entire project, from development to installation and operation. Dr. Carlo Bottasso discussed needs and tools to better define and understand the effectiveness of innovations for wind turbine systems. Automated design methods, while not replacing the role of the expert designer, help explore with confidence the solution space and evaluate all the necessary trade-offs across all components. Dr. Andrew Ning highlighted important aspects of optimization problems for wind turbines. His talk focused on understanding the importance of optimization objectives and constraints, explaining how sequential aero/structural optimization would yield suboptimal results compared to fully integrated optimization. Dr. Ryan Schkoda introduced the new Wind Turbine Drivetrain Testing Facility in Charleston, SC. The test benches are complex electrical-mechanical-hydraulic-systems intended to assess performance of entire nacelle assemblies under a variety of loading conditions.
- Joaquim Martins, Ph.D. University of Michigan
Towards Optimal Aeroelastic Tailoring of Wind Turbine Blades - Curran Crawford, Ph.D. University of Victoria, Canada
Progress towards a mid-fidelity wind turbine MDO capability for advanced aeroelastic rotors - Turaj Ashuri, Ph.D. University of Michigan
Aeroservoelastic design optimization of large wind turbines
Summary: This session provided additional perspectives on multi-disciplinary design analysis and optimization. The presentation by Dr. Ashuri highlighted his PhD work in MDO for a wind turbine integrating NREL's FAST and other codes. He completed this work through funding from Siemens for his PhD at TU Delft in the Netherlands. Dr. Martins' presentation focused on relatively new work looking at MDO for wind drawing extensively from his experience in the aerospace sector and focusing on blade design in particular. Dr. Curran Crawford finished the session with a presentation on additional MDO work applied to integrated wind turbine aerodynamic and structural design. Overall, the session highlighted the growing activity in MDO for wind energy applications for various subsystems and overall turbine design.
Wednesday — January 30, 2013
- Maureen Hand, Ph.D. NREL Strategic Energy and Analysis Center
Wind Plant Cost of Energy: Past and Future - Henk-Jan Kooijman, Ph.D. GE Energy
Keynote Address: Opportunities to reduce the cost of wind energy
Summary: The second day opened with a focus on big picture issues, highlighting the overall motivation of a systems approach by looking at global wind plant levelized cost of energy (LCOE) trends. Dr. Maureen Hand of NREL provided an overview of LCOE trends historically for a number of countries and then discussed different methods for projecting LCOE for future wind plants and technologies. She provided some background on three different approaches: learning curves, expert elicitation and engineering-based analysis; all of which have an important role to play in assessing future potential energy costs. Continuing on with the theme of LCOE, Mr. Henk-Jan Kooijman of GE Energy discussed from a high-level perspective how wind energy costs may be reduced by different innovations with particular emphasis on taking the system into account when evaluating the impact of such innovations. His talk highlighted some key technologies in the space of turbine design standards, resource assessment, and plant operations.
- Gianluca Iaccarino, Ph.D. Stanford University
Computational Strategies for Aerodynamic Design and Analysis in the Presence of Uncertainties - Mike Eldred, Ph.D. Sandia National Laboratories
Advances in UQ Algorithms for Wind Energy Applications
Summary: The focus of this session was on the application of Uncertainty Quantification (UQ) to wind turbine and wind farm design. Dr. Iaccarino demonstrated the application of UQ to high fidelity analysis of Vertical Axis Wind Turbines. Dr. Eldred presented details on how to account for both epistemic and aleatory uncertainty in the design process with the DAKOTA software. The central theme of both presentations was the large effect that uncertainty can have on the overall design of a wind power system and how that mandates the application of UQ to properly account for it. The most common, and simplest to execute, UQ technique involves a statistical sampling method with thousands (or hundreds of thousands) of samples to converge to a valid answer. This can be extremely computationally expensive, and Dr. Eldred discussed several more advanced UQ methods that can provide answers within hundreds of function evaluations. These methods open the door for the use of UQ for design under uncertainty as an integral part of the design process.
- Chris Halse, Ph.D. Romax Technology
Wind Turbine Drivetrain Development - Eddie Mayda, Ph.D. Siemens Energy Inc.
Blade Design at Siemens Wind Power: Experiences from Industrial Application of MDO - John Leahey, Vestas — American Wind Technology, Inc
Applications of Concurrent Engineering (CE) in Wind Turbine Design - Charu Mehendale, Ph.D. GE Global Research
GE Perspective on Wind Systems Engineering
Summary: To begin this session, Charu Mehendale summarized the diverse systems engineering tools and methods used by GE for evaluating new technologies and for designing next-generation products. He noted the potential for system engineering tools at the component, turbine, and wind plant levels. John Leahy highlighted the advantages of concurrent engineering, including improved product quality and reduced cost, and explained how concurrent engineering relates to systems engineering. Eddie Mayda spoke about the complex multi-disciplinary, multi-objective design of wind turbine rotors, how the process has become substantially more complex, and must be solved faster, better and cheaper than ever before. A description of the multi-disciplinary optimization (MDO) framework at SWP was presented, including their "multi-objective" strategy and some recent success stories. Christopher Halse discussed how wind turbine drivetrain main shaft, main bearings, gearbox, high speed coupling and generator need to be designed together. Methods were described for physical modeling of the drivetrain system aimed at understanding how components interact in terms of loading, misalignments, dynamic responses and failure rates.
- Jim O'Sullivan, Technip
Offshore Wind System Design — Lessons Learned From the Oil and Gas industry
Summary: Jim O'Sullivan's keynote address provided the oil and gas perspective to convey the experience that may be applicable to offshore wind systems. It was full of energy and kept the audience's attention on how things are done in the oil industry, including lessons learned. Economics require outside the box thinking to make offshore wind commercially viable. The idea that stuck to most is the fact that going offshore is about 3 times the cost of generating electricity from onshore wind facilities.
- Philippe Giguère, GE Energy
Wind Turbine Layout and Performance Optimization — A Manufacturer's Perspective - Matt Churchfield, Ph.D. NREL National Wind Technology Center
An Overview of SOWFA — The Simulator for Off/Onshore Wind Farm Applications - Jake Frye, DNV KEMA Energy and Sustainability
Layout optimization's influence on project risk
Summary: This session had participants from three industry sectors: manufacturer (Phillipe Giguerre), research (Matt Churchfield), and consultant/due diligence (Jake Frye). Each speaker gave his perspective on wind farm development and operation. Phillipe's talk focused on the importance of international design standards and structural loading of turbines. Matt talked about the importance of wake modeling with optimizing a layout. New models are needed although current high fidelity models are not necessarily more accurate than lower fidelity ones. Jake gave the consultant's perspective of checking both the manufacturers and wind farm developers designs and assumptions. Turbines are often placed in locations close to their design margins and uncertainty plays an important role in the process. Reductions in uncertainty have the potential to reduce the cost of energy in a number of ways.
- Matt Filippelli, AWS Truepower
Wind Project Design and Optimization: Introduction, Validation, and Applications of openWind - Scott Haynes, Iberdrola Renewables
Wind Farm Design — A focus on real world development and constraints - Matthew Lynn, GL Garrad Hassan
Layout Optimisation — What Are We Optimizing and How?
Summary: Session VII presented perspectives on layout optimization from developers, OEM's, and third party engineers. Matt Filippelli presented on the design and validation of AWS Truepower's openWind tool, and in particular discussed the available wake models, including a Deep Array Wake Model, and optimization techniques that included balance of station costs. Scott Haynes discussed wind plant layout design from the developer's perspective and emphasized the iterative process and lengthy timescales inherent to wind farm development. Matthew Lynn presented a case study demonstrating the spatial constraints that must be observed in wind plant design. In addition, he discussed challenges in modeling stable atmospheric conditions and offered research results that showed CFD simulations of stable atmospheric conditions were in better agreement with observations than a simple linear windflow WAsP run. The Q&A period featured a discussion that juxtaposed the constraints and optimization of onshore and offshore wind farm development.
- Katherine Dykes, NREL National Wind Technology Center
Analysis of Wind Plant Cost with NREL's Wind Energy Systems Engineering Software - Frederik Zahle, Ph.D. DTU Wind Energy, Denmark
Towards an integrated design complex for wind turbines - Pierre-Elouan Réthoré, Ph.D. DTU Wind Energy, Denmark
Wind Farm Design and Optimization — Presentation of TOPFARM and EERA-DTOC
Summary: The focus of this final session was on a set of approaches for integrated wind turbine and plant modeling. In the first talk, Katherine Dykes spoke about the NWTC's efforts in developing a new software tool for the research, design, and development of wind energy systems. This tool—specifically focused on integrating engineering and cost-based analysis tool—will represent a full wind plant, allow interchangeable models of varying fidelity, and support a wide variety of analysis. Dr. Frederik Zahle spoke about the Light Rotor Project, which is a 10 MW reference turbine that involved the collaboration of aerodynamic, aeroelastic, and structural experts. Dr. Pierre-Elouan Rethore focused on integrated design tools for wind farms, specifically the TOPFARM and EERA-DTOC projects. The first is concerned with creating a multi-fidelity framework for optimization of onshore and offshore wind farms. The second involves mesoscale wake effects for studying the effects of entire wind farms on neighboring wind farms. These talks represent a next generation of highly integrated multi-scale multi-physics multi-fidelity wind farm analysis and design tools.
- Paul Veers, Ph.D. NREL National Wind Technology Center
Publications
Read the Proceedings of Second NREL Wind Energy Systems Engineering Workshop.
Return to the Systems Engineering workshops page.
Share
Last Updated Feb. 14, 2025