Manufacturing and Additive Design of Electric Machines by 3D Printing
NREL's crosscutting research on advanced design optimization for three-dimensional (3D) printing of electric machines could enable next-generation, lightweight offshore wind turbine generators with reduced use of critical materials.
The research will transform the manufacturing infrastructure needed to meet the deployment goals for offshore wind in the United States.
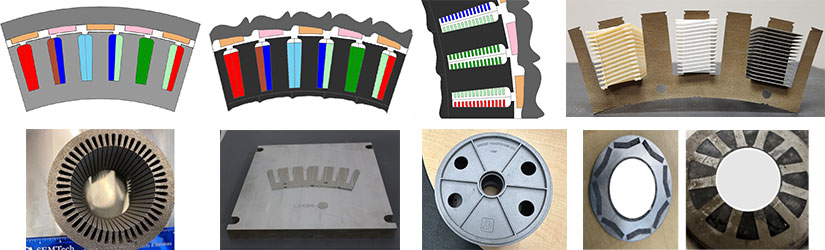
Project Background
At NREL, researchers are working on Manufacturing and Additive Design of Electric Machines by 3D Printing (MADE3D), a 5-year project that began in 2020. The project, funded through the U.S. Department of Energy’s (DOE’s) Wind Energy Technologies Office, is a collaboration among researchers at national laboratories (NREL and Oak Ridge National Laboratory), government agencies (NASA-Glenn Research Center), and industry (Bergey WindPower).
As the United States transitions to a large-scale clean energy economy with diverse renewable energy sources with minimal land impact, offshore wind will be a crucial player. With an ambitious target of 30 GW of wind power installation by 2030, and a surge in interest for larger turbines beyond 12 MW, innovations are needed in design and domestic manufacture of large turbines. We also need to address challenges of transportability and weight of large components and reduce raw material demand, considering soaring prices and supply chain shortages with limited manufacturing infrastructure. A needed area of innovation is efficient, reliable, high-power, dense generators with reduced rare-earth content. Direct-drive generators are popular but tend to use large amounts of magnets (>1T/MW) and scale disproportionately in terms of mass. This makes them prohibitively expensive (such generators can weigh over 300 tons and span more than 10 meters in diameter and introduce challenges for lifting and transportation by shipping vessels). Traditional design and manufacturing methods for lightweighting such generators offer limited opportunities to conserve rare-earth minerals and use processes that are environmentally unfriendly and result in excessive material waste.
Designing and manufacturing with supply chain considerations is more important than ever. Therefore, several wind original equipment manufacturers have announced new manufacturing facilities near port locations to reduce costs. They are pursuing new, efficient materials and designs to reduce critical material usage—especially of rare earth magnets, electrical steel, and copper—which could alleviate challenges in foreign sourcing of raw materials. As performance gaps exist with alternative materials, we need to find new ways of designing lightweight wind turbine generators with reduced rare-earth magnets that can match the performance of existing generators. Efforts are needed to enable such designs by innovative manufacturing with domestically sourced, cheaper magnet materials for wind turbines.
The goal of the MADE3D project is to enable better-performing electric machines that are lightweight and free of critical rare-earth elements by leveraging advances in magnet and metal additive manufacturing. Project researchers are doing this by exploring the full design space and improving near-net shaping using new powerful machine learning-enabled software and multimaterial additive manufacturing methods. The MADE3D team's efforts target high-power-density motors and generators in technologies across industries, including:
- Large offshore wind turbines
- Electric aircrafts
- Naval platforms and ships
- Electric drives in cars and other automobiles.
The team approached the project in multiple steps.
- It examined the potential for weight reduction using advanced optimization techniques for a 15-MW and 15-kW direct drive generator.
- It developed two new methods for magnetic topology optimization leveraging 3D-printed magnet materials: aIt s grid-based topology optimization and a grid-free shape optimization.
- It made available a new magnetic topology optimization software, MADE3D-Advanced Machine Learning©, which uses physics-informed machine learning models for training and generator performance prediction for new topologies for a given target torque and mass reduction. The toolset greatly accelerates the design space exploration in identifying new, advanced designs that are lightweight and can be single or multimaterial.
- The MADE3D-Advanced Machine Learning toolset helped identify a more than 15-ton reduction in rotor electrical steel mass (more than 50% reduction in rotor electrical steel mass) from the baseline 15-MW direct drive generator.
- The toolset was extended on a commercial baseline 15-kW generator by Bergey Wind Power Co. and helped identify up to 35% magnet mass reduction with 1% improvement in efficiency when compared to the baseline machine. Further, the presence of polymer binder in printed magnets make them up to 30% cheaper than sintered magnets. From a raw-materials cost perspective, this will serve as a major incentive to use polymer-bonded magnets in wind turbine generators.
- It advanced Dy-free NdFeB polymer-bonded magnets with a 75% volume higher magnetic loading and an energy product of up to 20 MGOe using the BAAM system. Further research with reduced polymer loading and metal additives can pave the way for higher energy products of up to 30 MGOe.
- It advanced laser powder bed-based printing technology for printing electrical steel laminates for a 15-kW generator with properties comparable to baseline electrical steel laminates.
- It developed a new extrusion-based printing, followed by insert molding, for multimaterial printing of magnets with electrical steel. The method will simplify the magnet assembly process by eliminating the need for adhesives.
- It evaluated candidate conductors (copper, silver-coated copper and silver, and compounded silver and copper) and insulation materials. It also developed a method for multimaterial printing of electrical conductors with insulation using a direct-ink write method.
- It evaluated the technical readiness of state-of-the-art commercial printers, the material handling capabilities, and the gaps and challenges in scaling the lab-developed processes for printing stator laminations, electrical conductors, rotor core, and magnets.
- Identified indirect additive manufacturing (sand printing followed by casting) as the most cost-effective production for rotor core. Current costs to print stator laminations are high, owing to high energy consumption for laser power and scan speed for achieving the best magnetic properties. Further R&D on print parameter optimization can help lower printing costs.
The team is looking ahead to next steps to get the technologies developed to commercialization:
- 2025–2027: Design, build, and validate a proof-of-concept prototype electric machine with reduced rare-earth magnets
- 2027–2030: Expand to other industries by advancing magnet and conductor technologies.
- 2030–Beyond: Integrate into production lines for industry adoption.
This project received feedback and inputs from an expert advisory board comprising experts from the industry, including General Electric Vernova, Siemens Technology Corp., ABB, and Arnold Magnetics. The team is continuing to work with government agencies (DOE Wind Energy Technologies Office, DOE Advanced Materials and Manufacturing Technologies Offices, and NASA-Glenn), original equipment manufacturers (Bergey WindPower), 3D printer manufacturers (Renishaw, Volunteer Aerospace, ExOne, and Additive Drives), and GmBH.
NREL: DiLea Bindel, Ganesh Vijaykumar, Jonathan Keller, Andrew Glaws, Miles Skinner,
Hannes Labuschagne, Lee Jay Fingersh
Oak Ridge National Laboratory: Parans Paranthaman, Haobo Wang, Willie Kemp, Tej Nath
Lamichhane, Kaustubh Mungale, Uday Vaidya
NASA-Glenn: Michael Halbig, Mrityunjay Singh, Zachary Tuchfeld
Bergey Wind Power Co.: Tod Hanley, Mike Bergey
Patents
A software record, SWR-20-70 for MADE3D-AML has been asserted with a closed-source copyright.
A nonprovisional patent application—invention disclosure record number: 2532 with the United States Patent and Trademark Office.
U.S. Patent No. 11,993,834 Issued: May 28, 2024 , “Indirect Additive Manufacturing Process For Fabricating Bonded Soft Magnets.”
Publications
Advanced Permanent Magnet Generator Topologies Using Multimaterial Shape Optimization and 3D Printing, 12th International Conference on Power Electronics, Machines and Drives (2024)
Advanced Multimaterial Shape Optimization Methods As Applied To Advanced Manufacturing of Wind Turbine Generators, Wind Energy (2024)
Final Technical Report: Manufacturing and Additive Design of Electric Machines by 3D Printing (MADE3D), NREL Technical Report (2024)
Novel Method For Overmolding of NdFeB Bonded Magnets Into a 3D-Printed Rotor, IEEE Transactions on Magnetics (2024)
Advanced Permanent Magnet Generator Topologies Using Multimaterial Shape Optimization and 3D Printing, NREL Presentation (2023)
An Assessment of Additively Manufactured Bonded Permanent Magnets for a Distributed Wind Generator, IEEE International Electric Machines and Drives Conference (2023)
A New Shape Optimization Approach for Lightweighting Electric Machines Inspired By Additive Manufacturing, Joint MMM-Intermag Conference (2022)
Review of Additive Manufacturing of Permanent Magnets for Electrical Machines: A Prospective on Wind Turbine, Materials Today Physics (2022)
MADE3D: Enabling the Next Generation of High-Torque Density Wind Generators by Additive Design and 3D Printing, Springer Nature (2021)
View all NREL publications about MADE3D research.
Contact
Share
Last Updated Feb. 25, 2025