Electric Motor Thermal Management
NREL's electric machine thermal management research generates experimental data and simulation processes for the modeling, analysis, design, and construction of new electric machines for vehicles.
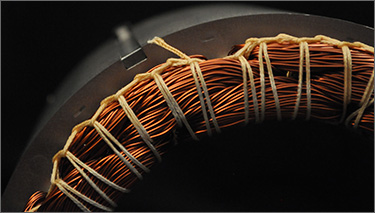
NREL research in electric motors improves the performance and reliability of electric-drive vehicles. Photo by Kevin Bennion, NREL
NREL research helps us better understand and evaluate the material and interface properties of electric machines as a function of temperature. Researchers also develop and evaluate advanced fluid-based electric machine cooling strategies for improved performance and reliability of electric vehicles.
Industry partners want to better understand heat transfer in electric machines to develop motors that reliably operate with reduced size and cost. NREL research addresses this challenge and supports broad industry demand for data, analysis methods, and experimental techniques to improve electric machine thermal management.
Capabilities
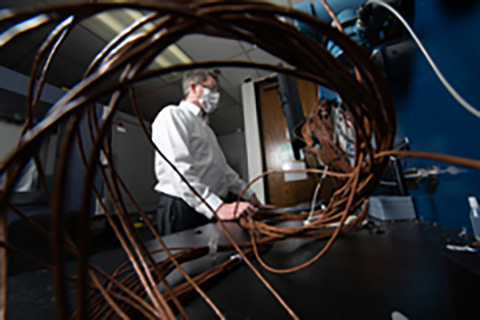
Kevin Bennion operates the water-ethylene glycol test loop to evaluate cooling technologies for electric machine thermal management. Photo by Dennis Schroeder, NREL
Research to characterize and improve electric machine thermal management includes:
- Developing fluid-based (transmission oil, water-ethylene glycol) cooling technologies for the stator and the rotor
- Characterizing automatic transmission fluid impingement and flow on geometrically representative surfaces and providing validated computational fluid dynamics models
- Performing passive stack thermal characterization and improvements for the stator and the rotor, including laminations, end-windings, and slot-windings
- Collaborating with other national laboratories and industry partners to measure thermal performance of materials, improve motor performance and thermal management, and facilitate future bench-level thermal evaluation of electric motor components
- Supporting thermal management design for motors developed by NREL partners.
Share
Last Updated Feb. 28, 2025