Fuel Chemical Analysis and Properties Research
NREL strives to more deeply understand how fuel properties impact engine operation efficiency and emissions. We accomplish this by relating fuel properties to fuel chemistry and molecular structure.
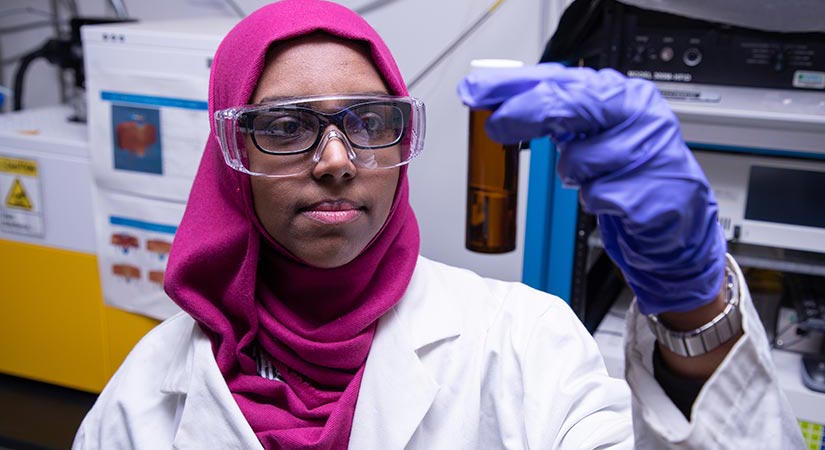
Photo by Joe DelNero, NREL
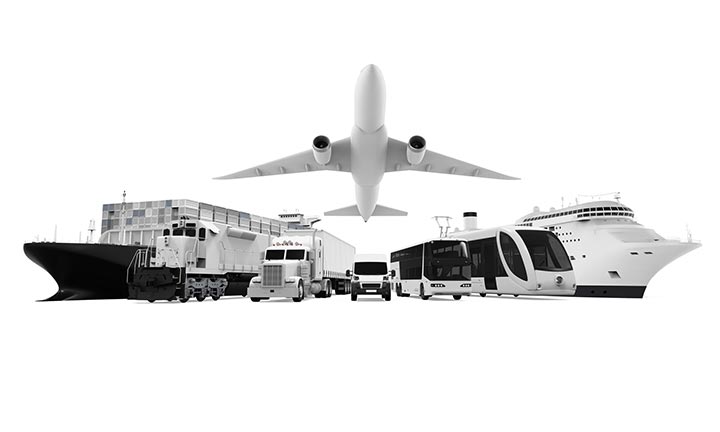
Through fundamental kinetics, high-performance computing simulations, and high-fidelity combustion simulations, we provide the crucial connection between fuel properties and molecular structure so fuel producers can target design and production of fuels with the right chemistry for the intended application.
Types of Fuel Chemical Analyses
We evaluate a range of fuels, including gasoline, diesel, jet, and marine.
- Research octane and motor octane number
- Reid vapor pressure
- Heat of vaporization (HOV) via a novel in-house method
- Distillation
- Oxidation stability
- Detailed hydrocarbon analysis (DHA)
- Cetane number
- Cloud point + related methods
- Simulated distillation
- Viscosity
- Oxidation stability
- Jet fuel speciation (GCxGC time-of-flight mass spectrometer)
- Freezing point
- Simulated distillation
- Cetane number
- Heat of combustion
- Surface tension at a temperature range of -35°C–400°C and pressure range of 1–80 bar
- Viscosity at a temperature range of -40°C–315°C and pressure range of 1–80 bar
- Flashpoint
- Density at a temperature range of -10°C–200°C and pressure range of 1–500 bar
See information about our sustainable aviation fuels research.
- Acid number
- Density
- Flash point
- Pour point
- Viscosity
- Fuel blend stability
See information about our marine fuels research.
Detailed Hydrocarbon Analysis
The DHA-derived parameter particulate matter index (PMI) is a widely used metric for ranking the particulate matter formation tendency of gasolines, including gasolines containing biofuels. Particulate matter consists of fine particles that have negative impacts on human health. Their emissions from cars and trucks are regulated by government agencies worldwide.
PMI is calculated from the DHA, considering the properties of each individual component. NREL's fuel chemistry and engine combustion research has shown that particle formation from biomass-derived oxygenates is not accurately predicted by PMI because some oxygenates have low energy barrier reaction pathways to soot formation. For more information, see engine combustion research.
Additionally, alcohols such as ethanol have a much higher HOV than gasoline, and when blended into gasoline the increased evaporative cooling can cause more particles to form from the aromatic compounds in gasoline under some conditions. The DHA can also be used to calculate the HOV of complex mixtures such as gasoline-ethanol blends. Research is exploring how to predict the distillation curve of gasoline from the DHA as well as other properties.
For more information, read A Review and Perspective on Particulate Matter Indices Linking Fuel Composition to Particulate Emissions, SAE International Journal of Fuels and Lubricants (2022).
Novel Gasoline Heat of Vaporization Measurement Method
NREL has developed a method for measuring HOV as the fuel evaporates using a differential scanning calorimetry/thermogravimetric analysis (DSC/TGA) instrument. The method has been applied to market gasoline samples, as well as blends of alcohols in gasoline, and has been modified to provide the HOV of diesel-boiling range components. A high-pressure DSC is utilized to provide enthalpy diagrams of jet fuel.
Our combined DSC/TGA and high-pressure DSC capabilities can be used to generate these data, including the heat capacity at constant pressure versus temperature measurements.
Advanced Fuel Ignition Delay Analyzer
The research-grade Advanced Fuel Ignition Delay Analyzer (AFIDA), a constant-volume combustion chamber platform for fuel ignition kinetics research, was acquired to expand capabilities in screening small quantities of fuel compound candidates. This equipment significantly increases the range of experimental conditions and throughput to map ignition delay of novel fuel compounds and blends. The AFIDA offers greater experimental flexibility compared to NREL's Ignition Quality Tester (IQT) platform; a high-pressure (1,200- bar) direct-injection system to minimize spray physics effects; and an autosampler carousel to enable automatic operation for experiments with various fuels, pressures, and temperatures.
Ignition Quality Tester
The IQT is a constant volume combustion vessel that is used to study ignition properties of liquid fuels. In addition to the main combustion unit, the IQT includes temperature controllers and other electronics and a closed-loop cooling system. A high-speed pressure transducer measures chamber pressure to detect fuel ignition. Fuel samples are injected into the combustion chamber through a pintle-type injector nozzle.
Publications
Read about related studies and browse all NREL publications about fuel chemical analysis and properties R&D.
A Review and Perspective on Particulate Matter Indices Linking Fuel Composition to Particulate Emissions, SAE International Journal of Fuels and Lubricants (2022)
Heat of Vaporization and Species Evolution During Gasoline Evaporation Measured by DSC/TGA/MS for Blends of C1 to C4 Alcohols in Commercial Gasoline Blendstocks, SAE International Powertrains Fuels & Lubricants Meeting (2019)
Contact
Share
Last Updated Aug. 15, 2025