Leading by Example: ITEAM Prize Recognizes Energy-Saving Excellence at U.S. Manufacturing Plants
Setting a good example for others can prompt a domino effect that leads to lasting change—in fact, the U.S. Department of Energy (DOE) is betting on it.
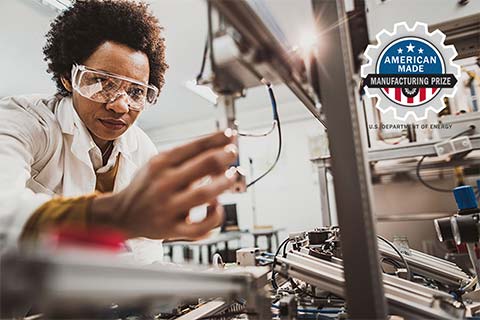
Today, DOE’s Advanced Manufacturing Office announced winners of the Individuals Taking Energy Action in Manufacturing (ITEAM) Prize. Part of the American-Made Challenges series, the ITEAM Prize launched in 2018 with the goal of recognizing employees at U.S. manufacturing facilities around the country who are energy-saving superheroes.
With this prize, DOE celebrates leaders who are responsible for creative, specific, and innovative projects to drive measurable energy savings in their manufacturing plants, from implementing contests that identify compressed air leaks to spearheading efforts to retrofit or replace outdated manufacturing equipment.
Each winner is awarded a cash prize of $5,000 and will be recognized at the virtual Association of Energy Engineers World Energy Conference and Expo. Winners will also have their ideas and practices highlighted on the Better Buildings Solutions Center website to serve as inspiration for all U.S. Manufacturing facilities from coast-to-coast.
Rethinking Business as Usual
Applications were evaluated on demonstrated energy savings, with extra credit awarded for strategies that engaged other workers on the manufacturing floor. Eight winners were selected from small-, medium-, and large-size manufacturing facilities.
Let’s learn a bit more about these trailblazers and their winning ideas.
- George Anglin at Toyota Manufacturing, Texas, applied the Toyota Production System tenet of “use what you need, when you need it, in the amount you need.” Anglin worked to identify opportunities for energy-efficient equipment installation and best practices to achieve energy reductions while maintaining quality standards. By swapping in LEDs and installing higher-efficiency heating, ventilation, and air-conditioning (HVAC) systems at the plant’s medical office building, Anglin helped the plant save 1.27 megawatt-hours (MWh) and nearly $89,000 annually.
- Electrical Supervisor Jeff Feyen of Saukville, Wisconsin’s Charter Steel, examined energy consumption and waste, helping to ensure this focus was integrated into everyday culture at his plant. With an eye to lighting upgrades, installation of variable-frequency drives (VFDs), compressed air and heating usage, and more, Jeff has helped save his processing plant 6% of its energy usage, or more than 81,000 MMBTUs (one million British Thermal Units).
- The Kingsport, Tennessee, Eastman facility has Power Department Staff Engineer Marcus Johnson to thank for achieving significantly lower fuel consumption and a more than 4% improvement in the efficiency of two 60-year-old coal-fired stoker boilers. Spearheading the boiler efficiency improvement effort, Johnson helped demonstrate the value of efficiency, showing that energy costs are affected by how well the equipment is run, maintained, and understood. Johnson formed an Equipment Performance Team to share lessons learned that could be applied to the site’s 17 boilers and 19 turbo generators.
- Over the last 20 years, Manufacturing Engineer Terry McMichael of 3M’s Cynthiana, Kentucky, plant has led various energy efficiency projects that have amounted to a savings of more than $5 million at the plant. Terry worked to ensure the correct size air compressors were employed at the plant, as well as implemented efficient sequencing of the compressors, and pinpointed and systematically fixed air leaks, saving the plant $40,000 and 1.1 MWh of source electricity.
- Mike Rogers, Site Utilities Coordinator at 3M’s Cottage Grove, Minnesota, plant led the site’s efforts to become ISO 50001 certified. Spanning 1.5 years, the project saw the implementation of the Energy Management System (EnMS) and achievement of ISO 50001 certification. In the first year of implementation, Cottage Grove exhibited a 1.5% increase in energy cost savings and $59,000 in savings as compared to the previous year.
- Rochelle Samuel created the Compressed Air Challenge while she was a member of the Saint-Gobain North America Environmental, Health, Safety, and Sustainability team. The competition challenged 22 teams across 19 sites to identify and fix compressed air leaks, as well as enable a sustainable compressed air operations and management system. The participating sites identified 837 leaks of varying sizes and repaired 48% of them, representing 26 gigawatt-hours (GWh) and $2.5 million in potential annual energy savings for the company.
- Nick Sayles acted as a “Sustainability Champion,” a role created across Saint-Gobain North America plants to reduce environmental impacts of their operations. Sayles and his team developed an on-site competition to uncover compressed air leaks at their plant. As a result of this innovative competition, the team fixed 96 of the 100 air leaks identified over the course of the 3-month competition, the savings of which is approximately 254 cubic feet per minute, or $10,000 annually.
- David Turkes, of commercial carpet manufacturer Bentley Mills, was nominated for his energy efficiency lighting retrofit project. The retrofit of approximately 3,455 fixtures resulted in an annual savings of 1.6 million kilowatt-hours (kWh), or roughly 30% of their annual electricity consumption. Bentley Mills, a Los Angeles-based company, is the first carpet company to receive a LEED designation and considers sustainability core to their operations.
DOE also recognizes the following project with an honorable mention:
Andy Hopkins, John Henry, Marc Matsen, Chris Hottes, and James Kestner at Boeing for implementing energy-saving changes to how their thermoset composite 787 horizontal stabilizers are produced at Boeing’s West Jordan, Utah, plant. By employing the de-bulk system in place of using an autoclave, the plant was able to reap a 99% savings in energy for this step of production.
Energy Savings and a Better Bottom Line
Adopting energy-saving practices and procedures do more than save energy—they also allow companies to strengthen their competitiveness and reduce their bottom line.
Energy efficiency is contagious. DOE hopes that by sharing energy productivity success stories, and shining a spotlight on the leadership behind them, that other manufacturing facilities around the country will follow suit and adopt similar sustainability strategies and technologies.
Learn more about ITEAM Prize and the DOE Advanced Manufacturing Office and how you, too, can become a leader in energy efficiency innovation.