New Materials Could Lead to Recyclable Wind Blades
Advancements in wind energy have allowed the amount of carbon emitted into the atmosphere to drop considerably, and all without raising the levelized cost of energy. However, disposing of the materials used to create these energy-efficient machines can be complicated and have unintended consequences. Thanks to researchers at the NREL, this could soon be a thing of the past.
Recycling existing thermoset materials—commonly used in wind blades—is challenging, so NREL researchers Robynne Murray and Derek Berry are investigating a new composite of reactive thermoplastics as a replacement. These thermoplastics have three key benefits over their predecessors:
- They are recyclable at the end of a blade's life.
- They are less expensive to manufacture.
- They enable thermal joining and shaping, which is a lighter and potentially more reliable manufacturing process.
Manufacturing Game-Changers
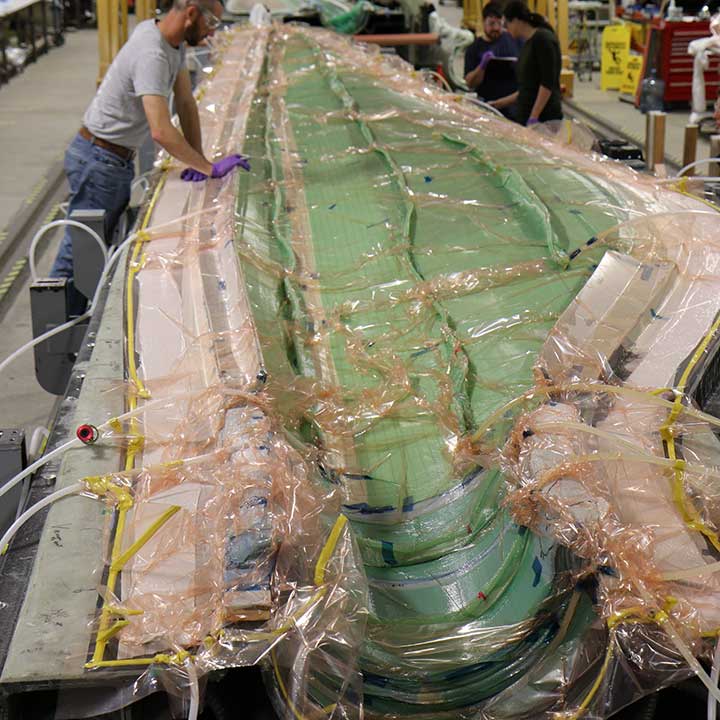
The team works to develop a blade using recyclable thermoplastic material. Photo by Dave Snowberg, NREL
Murray and a team of NREL researchers are exploring the manufacturing process for specific parts of a thermoplastic wind blade. In a recent article published in the journal Applied Composite Materials, the team noted that significant improvements in energy savings can be achieved by recycling retired materials and using thermal welding practices. In addition, thermoplastic materials have a room-temperature cure and require no post-cure steps, which is a huge improvement over traditional epoxy thermoset materials that require expensive heated molds and an energy- and time-intensive post-cure oven procedure.
"Since thermoplastics can be easily heated and formed, they also have the potential to be repaired in the event of damage," said Murray. "The repairability and reduced space and manufacturing time requirements of thermoplastic blades make them a promising option for on-site manufacturing." By allowing for on-site development and repairs, supply chain logistics and costs are dramatically reduced for wind plant owners and operators.
Given these potential savings, the NREL team did extensive research and published the results on the overall technoeconomic impacts of thermoplastic blades. There are clear cost savings in the manufacturing process, but potential savings could also be found by thermally welding the materials, ultimately reducing blade weight and cycle times.
As blade materials become recyclable, repair and decommissioning costs will decrease as well. "Eventually, recycling thermoplastic wind turbine blades could become a revenue generator for wind turbine farm owners and operators," said Berry.
These benefits all show promise on a small-scale, theoretical level, but real impact is seen at commercialization. So far, only blades between 9 and 20 meters long have been manufactured using these thermoplastic resins, and average utility-scale blades today are up to 50 meters in length. In another publication by the team, results show that traditional epoxy thermoset materials and thermoplastics perform similarly in small-scale models. This positive result warrants further research, potentially leading to full-scale experimentation.
Arkema, NREL's industry partner and the thermoplastic resin system supplier, is taking the next step and validating three 25-meter thermoplastic blades on a wind turbine in late 2019. This experiment will help prove the practicality of this technique. "Commercialization and industry use of thermoplastic resins in wind blades is the ultimate goal of this research," said Berry.
A completed thermoplastic blade, ready for validation. Photo by Dave Snowberg, NREL
NREL is working on some new research as well. A new internally funded project on thermal welding has begun. "Thermal welding technology has the potential to be game-changing in the way that blades are bonded, resulting in weight, time, and cost savings," said Murray. The team is manufacturing a 13-meter thermoplastic blade of their own in the Composites Manufacturing Education and Technology Facility and is focusing on fusion joining using this same thermoplastic resin.
NREL worked with a range of partners from the Institute for Advanced Composites Manufacturing Innovation on this research, including: Arkema, Colorado School of Mines, Johns Manville, Oak Ridge National Laboratory, Purdue University, TPI Composites, University of Tennessee, and Vanderbilt University. The research is supported by the U.S. Department of Energy Office of Energy Efficiency and Renewable Energy's Advanced Manufacturing Office. Additional supporters include the State of Colorado Office of Economic Development and International Trade, and the Institute for Advanced Composites Manufacturing Innovation.
Last Updated May 28, 2025