Copper Is King, But It Is Time for a Metal Meritocracy
These 4 Teams Are Building a Better Copper (or Trying To Replace It) To Supercharge the Future of Energy
For more than a century, copper has been the key material in electrical devices and wires, transporting electrons from sockets to smartphones and from batteries to electric vehicle motors.
Copper dominated for good reason. The metal is abundant and one of the most conductive, surpassed only by silver. Copper’s most dogged competitor, aluminum, is lighter and less expensive, making it a practical choice for power lines. But aluminum is about half as conductive as the king.
Today, as the world scrambles to slow climate change by electrifying everything (and decarbonizing everything), demand for copper is soaring, pushing prices higher. To deliver electricity to consumers faster and shed fewer electrons along the wiry way, the country must find new materials and smart manufacturing methods that can either enhance or replace king copper.
That is why the U.S. Department of Energy’s Advanced Materials and Manufacturing Technologies Office (AMMTO) launched a new prize in 2021. Through the $4.8 million Conductivity-enhanced materials for Affordable, Breakthrough Leapfrog Electric and thermal applications (CABLE) Conductor Manufacturing Prize, teams of researchers and inventors compete to create materials that can out-conduct pure copper.
In April 2023, the CABLE Prize crew selected seven teams to move on to the third and final stage of the competition. All seven are part of the country’s wide network of inventors, entrepreneurs, and innovators and hail from academia, industry, startups, and more. And four of these seven teams are working to “Beat Copper,” as the prize calls it.
We talked to all four teams to hear how their contenders—some of which still rely on smaller amounts of copper—could topple the metal monarchy.
“It’s Really a Miraculous Technology”
Team Name: Selva Research Group
Project Title: Super-Cool Superconductor
Institution and Location: University of Houston (Houston, Texas)
Slogan: “Infinite conductivity at half the cost of copper”
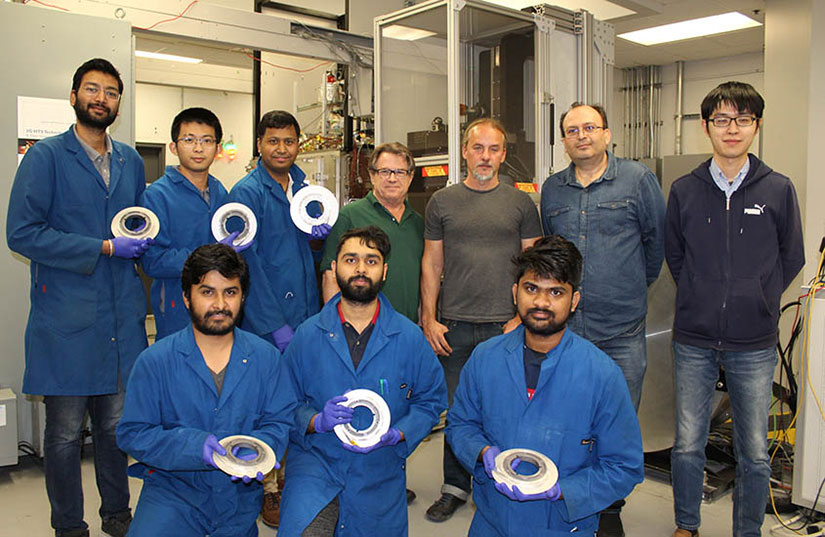
In 1987, Venkat Selvamanickam (who goes by Selva) was in the right place at the right time.
Selva had just started his graduate studies in mechanical engineering at the University of Houston when one of the physics department’s faculty members discovered the first high-temperature superconductor that can function using liquid nitrogen. Unlike traditional conductors, superconductors can offer electrons free, uninhibited passage through a wire; because electrons meet zero resistance, these materials can provide almost infinite conductivity.
“If you’re looking for high conductivity materials, there’s nothing better than a superconductor,” Selva said. His CABLE Prize goal is to replace, not improve, king copper.
Before 1986, superconductors could only function at super-low temperatures—specifically, just above absolute zero on the Kelvin scale—which are super expensive to reach. High-temperature superconductors can operate at about 100 Kelvin, far above absolute zero (although that’s still 200 Kelvin below the freezing point of water). These more practical superconductors could revolutionize the energy industry, enabling them to reduce both material and energy waste as well as carbon emissions. These super wires could even create the foundation for levitating trains, super-efficient microelectronics, and quantum computers.
But there was a problem.
Even if these high-temperature superconductors were cheaper to keep cool compared to their low-temperature cousins, the material was brittle. Most researchers believed the material was simply too fragile to be manufactured into an affordable product.
Most researchers—but not Selva.
Already, Selva’s superconductor costs eight times less to make than similar commercial products. That, and advances in cooling technology, could further reduce the cost and increase the reliability of all high-temperature superconductor systems.
Today, Selva is still at his alma mater, the University of Houston. But now, he is the M.D. Anderson chair professor of mechanical engineering, the director of the Advanced Manufacturing Institute, and the director of the Texas Center for Superconductivity Applied Research Hub. For the CABLE Prize, his lab, along with collaborators at AMPeers, LLC, are designing what Selva calls a “super-cool superconductor” that is half the cost of copper and far more conductive (when cooled).
When wired up with superconductors, clean energy technologies, like wind turbines, could generate more electricity with less material and weight. And all electric machines, including those that power cars and airplanes, would need less energy to operate.
“That will directly contribute to reducing carbon emissions,” Selva said.
But to make that widespread use possible, Selva continued, we must first bring down the cost of these super wires on a commercial scale. In Stage 3 of the CABLE Prize, he plans to manufacture longer pieces of his superconductor—which is mostly ceramic with some copper—to demonstrate that it can be super cool, super conductive, and relatively cheap, too.
“As soon as it’s cooled down to some nominal temperature, boom. It just becomes infinite conductivity,” Selva said.
Selva’s superconductor, which is based on the material discovered at the University of Houston in 1987, is not the only option out there. But it is still seen as the most reliable high-temperature superconductor. And cooling it down is not as hard as it used to be. Cooling wires with liquid nitrogen is relatively cheap (cheaper than a bottle of water), and new technologies, called cryocoolers, could make cooling even more affordable.
“It’s really a miraculous technology, in my opinion,” Selva said. “Even after all these years, I’m quite amazed at how well it works.”
“This Is Actually New Science”
Team Name: Team CoGrUW
Project Title: Copper-Graphene Ultra Wire
Institution and Location: MetalKraft Technologies, LLC (Albany, Ohio)
Slogan: “Powering the future with the invisible”
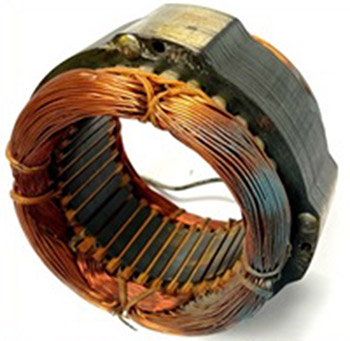
The COVID-19 pandemic was the push Frank Kraft needed.
Kraft was a mechanical engineering professor at Ohio University for more than 19 years and had already been thinking of leaving academia to launch his own startup. Then, the pandemic froze the educational system “literally overnight,” Kraft said.
“It gave me the push to do something else,” said Kraft, who is now the technical director of MetalKraft Technologies, LLC, which manufactures sleek-looking specialty copper tubes.
Now, Kraft wants to make an even sleeker kind of copper. He and his CABLE Prize team, which includes his son, Peter Kraft, and former Ohio University colleague, Keerti Kappagantula, a senior scientist at Pacific Northwest National Laboratory, are building their copper wires with a bit of graphene—an atom-wide layer of carbon that is highly conductive. Their goal is for their copper-graphene composite to best copper’s conductivity by 10%.
“Right now, most of our conductors are copper,” Kraft said. “That’s generally what we use for electric motors. And we’re limited by the electrical conductivity of that metal.”
Traditionally, engineers have made copper more conductive by removing impurities, which act like potholes in these electrical superhighways, impeding electrons from moving smoothly through the metal. By adding graphene to the copper, Kraft and his team are taking a counterintuitive approach: They’re adding carbon to enhance conductivity.
“This is actually new science,” Kraft said. “Some things need to happen on the atomic level—things that the physicists get excited about—to make all this happen.”
So far, the team’s novel material can beat copper’s conductivity by about 3%. But they hope that by the end of the CABLE Prize competition, they can reach the coveted 10%—the percentage that would give their metal enough of an edge to best copper.
Because even the purest copper has achieved almost no conductivity bump for over a century, any increase would be a breakthrough.
“We’re addressing the needs for the ever-increasing global electrification,” Kraft said. “Any device, such as electric motors, generators, transformers, and the like, we want to be able to make run more efficiently. And if we do that, the two big things would be energy savings—costs—but also for power plants, carbon emissions reductions.”
There is a third big thing: electric motors. “Everything runs on electric motors,” Kraft said. Industrial machinery uses massive electric motors, but smaller versions power electric vehicles, air conditioning systems, refrigerators and blenders, drones and gaming systems, MRI machines, and so much more. Even a small, say 5%, increase in energy efficiency could save huge amounts of energy (and, therefore, costs).
“If just 20% of all the electric motors were using ultraconductive wire, you could literally take power plants offline. It would be that much energy,” Kraft said. “There is definitely big potential.”
“Conduct Better Than Mother Nature Intended To”
Team Name: Team NAECO
Project Title: Conductivity-Enhanced Nanocarbon Copper Composite
Institution and Location: NAECO, LLC (Peachtree City, Georgia)
Slogan: “Innovation to help our planet”
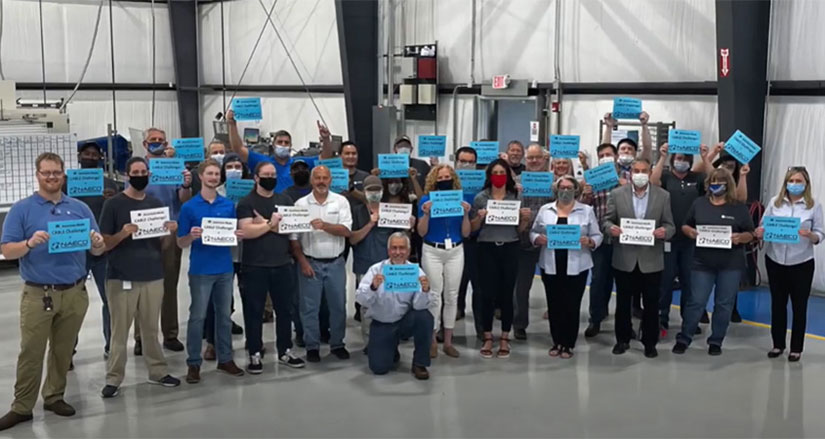
A moon-like disc of silvery metal framed David Bergmann’s head.
“It’s just a piece of metal art,” said Bergmann, the president of NAECO, LLC. “We’re not artists, but I like it. Reminds me of our products.”
Bergmann is a metal artist in his own way. With support from the CABLE Prize (and additional CABLE awards), he and his team are forging a new, more conductive wire by combining copper, a copper alloy (or impure copper mixture), and graphene.
But the stubborn metals do not always accept this forced union.
“It’s the easiest thing in the world to think, ‘Oh, I'll mix some of this carbon into the metal, like a chocolate peanut butter cup,’” said Bergmann. “It doesn’t work that way. It’s much, much more complicated or else it would have been done already.”
Metals, especially those that can conduct electricity, can sometimes resist combining with other elements. But if Bergmann and his team can force their metals and graphene to merge, that union could result in small but meaningful benefits. If every wire were just 5% or 10% more efficient at transporting electrons, then all electric technologies, including electric vehicles, could run longer or with less energy. And with more efficient conductors, the country can build lighter cables, wires, and batteries, which could save even more energy and cost.
“Airplanes have hundreds and hundreds of pounds of copper inside of them,” Bergmann said. “If you can make an airplane lighter, it would burn less fuel, go farther, or carry more people.”
A typical commercial airplane, for example, flies hundreds of flights per year, Bergmann said. One major airline reported that every pound removed from a commercial plane would save over a quarter-million pounds of jet fuel per year, “which is a huge lever for carbon dioxide emissions reduction,” said Bergmann.
“It’s a proven way to reduce everyone’s global carbon footprint,” said Bergmann.
He and his company are hoping to spread this efficiency wealth, lightening not just electric vehicles and airplanes but also freight and commuter trains. But first, Bergmann and team must scale up their novel wire to test it and make sure it’s an efficient and safe option, too.
“We’re focusing on building copper that can conduct better than Mother Nature intended to,” Bergmann said. “I could pick up the phone as soon as it’s ready and call 20 customers. They would all be beating our doors down.”
“It’s Too Good To Be True, but It’s True”
Team Name: University of Colorado Boulder
Project Title: Graphene Infused Copper Made by the Flash Method
Institution and Location: University of Colorado Boulder (Boulder, Colorado)
Slogan: “Ultra-high conductivity copper achieved by a simple manufacturing process”
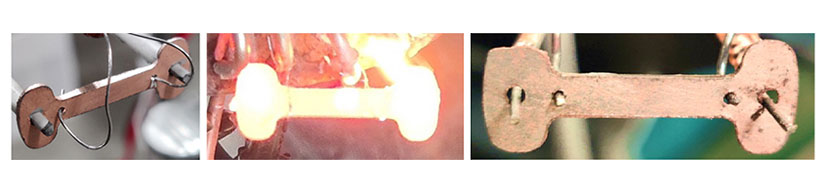
For Rishi Raj’s 75th birthday, his former students bought him a white ceramic duck about the size of a table lamp.
Today, five years later, the duck stares down at Raj from atop an overfull bookcase—a reminder not only of Raj’s half century of teaching but also of an invention more than a decade in the making.
“It started with ceramics, actually,” said Raj, a professor of materials science at the University of Colorado Boulder. “We call it flash.”
This specific flash process, which Raj and his lab members invented in 2010, is a novel way to forge new materials. The method creates a plasma in which chemical reactions can happen at astronomical rates to produce these finicky materials.
Now, Raj and Uthamalingam (Balu) Balachandran, a visiting professor at University of Colorado Boulder, in collaboration with the manufacturing company Prysmian Group, are exploring whether they can use flash to design more conductive copper wires for electric vehicles, planes, and even transmission systems.
“We got huge numbers,” Raj said. “We got numbers like—and I hesitate to say it, but why not?—greater than 110% of IACS [International Annealed Copper Standard].” For new cables to compete with today’s standard copper wires, the U.S. Department of Energy estimates that they must outperform copper by at least 10%.
“One of the reviewers said it is too good to be true, but it's true,” Raj said. “People have been trying for 100 years to get 102%. Even a 2% increase in conductivity would be valuable.”
Now, for the CABLE Prize, the team will try to reproduce their huge number on a larger scale. To build a bigger sample, they will use the flash process to infuse copper with graphene, which takes just seconds and can be done at relatively low temperatures.
Conventional processes often take hours and require heat of about 4,000 degrees Fahrenheit. Flash can get the job done at about 1,500 degrees Fahrenheit. And any temperature reduction can significantly cut the energy needed to manufacture these high-conductivity wires.
These flash materials come with an extra benefit, too: The graphene strengthens the copper. Even if the team’s long graphene-infused copper cables heat up from sunshine or the electrical energy coursing through them, they will not deform over time.
“It opens up new possibilities for manufacturing to produce high-conductivity copper,” Raj said. “And I am reasonably sure that, ultimately, it will succeed.”
Learn more about the CABLE Prize challenge and follow the teams’ progress!
Last Updated May 28, 2025