Stage 2 Winners of a Manufacturing Prize Are Supercharging U.S. Industries
After Extensive Materials Testing, 7 Teams Are Selected To Move on to Final Stage of the Prize
The Conductivity-enhanced materials for Affordable, Breakthrough Leapfrog Electric and thermal applications (CABLE) Conductor Manufacturing Prize is making big advances in the development of next-generation materials that could help upgrade and expand the country’s aging electric and transportation infrastructures.
Today, the U.S. Department of Energy (DOE) Office of Energy Efficiency and Renewable Energy named seven teams as winners in Stage 2 of the CABLE Conductor Manufacturing Prize, awarding each team $200,000 in cash and $100,000 in technical assistance vouchers.
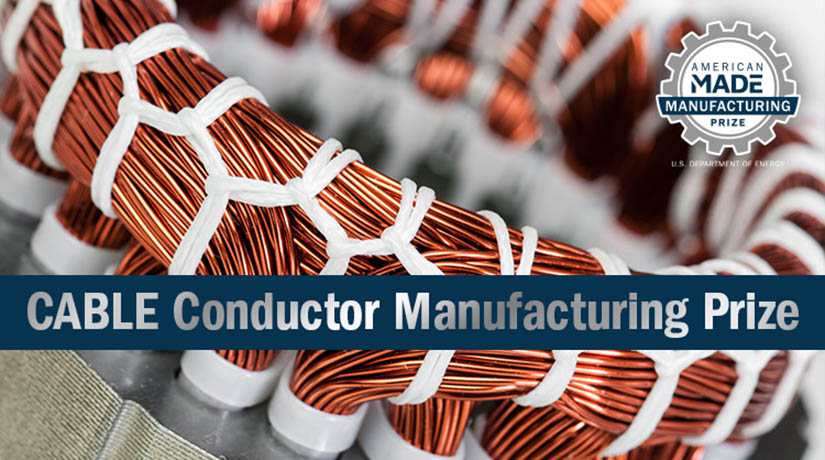
In this stage, competitors were required to submit a lab-scale sample of the material they presented in Phase 1 for electrical conductivity testing, along with preliminary plans to scale up and manufacture the material. The winning teams successfully demonstrated an improvement in conductivity above each contest baseline and exhibited the affordability, manufacturability, and commercialization potential of their materials.
“We knew going into Stage 2 that competitors were innovating some very promising materials concepts,” said Matt Ringer, the advanced manufacturing program manager at the National Renewable Energy Laboratory (NREL). “But seeing their samples tested in the lab demonstrated that these concepts are on the road to actually being marketable.”
Advancing Conductivity in Pursuit of a Carbon-Free Future
The CABLE Conductor Manufacturing Prize, which is run by DOE’s Advanced Materials and Manufacturing Technologies Office and administered by NREL, challenged materials inventors to demonstrate significant enhancements in materials’ conductivity and affordability that would enable U.S. manufacturers to leapfrog to next-generation materials.
The goal is to increase conductivity of mass-produced materials that could be used for electrical and/or thermal (heat-based) energy applications by at least 10% without increasing life-cycle cost. Even a relatively small percentage increase will dramatically lower manufacturing and energy costs and make it easier for the country to reach the levels of electrification needed to meet its goal of a carbon-pollution-free economy by 2050.
Even a relatively small percentage increase will be dramatically lower costs and impacts necessary to meet U.S. electricity demands as the country electrifies to achieve the goal of a carbon-pollution-free economy by 2050.
“To support electrification of everything from cars to home heating to manufacturing, our conductivity-enhanced materials need to be deployed faster and smarter,” said Tina Kaarsberg, a technology manager at DOE who oversees the prize. “We believe that recognizing breakthrough conductivity materials through this competition will accelerate innovation, lower costs, and enhance the community benefits of electrification.”
During Stage 2, competitors were judged not only on their material’s conductivity but also on their material’s ability to be economically competitive with the conductor systems it might replace, its status as a breakthrough, life-cycle resource use and carbon emissions, fabrication readiness, and proposed commercialization pathway.
Demonstrating Success in Stage 2
The winning technologies that best met the stage’s goals are:
- The Super Cool Conductor from the Selva Research Group in Houston, Texas, is made using a high-tech deposition and roll-to-roll process to create a superconductor film on a tape. This conductor could replace copper in motors, vehicle cables, and generators, and its magnetic properties also make it uniquely well suited to applications such as compact fusion power plants.
- The Graphene Infused Copper Made by the Flash Method made by the team from the University of Colorado at Boulder is made with a low-cost manufacturing process that can be completed in about 30 seconds without the need for a furnace.
- The Ultra-High-Strength/Highly Conductive Al Alloys made by the NanoAL Lightning Team in Ashland, Massachusetts could replace aluminum conductor steel-reinforced (ACSR) cables used in overhead transmission lines with an aluminum wire alloy that has higher conductivity and requires no steel because of its high tensile strength.
- The Copper-Graphene Ultra Wire from Team MetalKraft Technologies in Albany, Ohio, is made with a solid-phase process planned to be scaled to high-volume production that produces a wire more conductive than conventional copper wire.
- The Conductivity-Enhanced Nanocarbon Copper Composites from Team NAECO in Peachtree City, Georgia, are made by first mixing copper with trace amounts of additives before combining it with graphene in a solid-phase process.
- A Sapient Choice of Cables for Wind Energy superconductor from Team HyperTech in Columbus, Ohio, is made from low-cost materials in a scalable process. Because of the superconductor’s compact size, light weight, and magnetic properties, it could replace rare earth magnets in wind turbines, thereby making turbines more cost effective and/or reducing their tower size/weight.
- The Advanced Conductor with Conductive Strength Member, created by the TS Conductor Corporation in Huntington Beach, California, substitutes conductive carbon nanotube fibers for ACSR's steel reinforcement and many other manufacturing innovations for transmission lines.
These winning competitors will now move on to Stage 3—tentatively planned to open in fall 2023—in which they will manufacture a larger and more refined sample of their conductivity-enhanced materials and develop plans to commercialize their designs. At the conclusion of the final stage, planned for spring 2024, up to four winning teams will split a total prize pool of at least $2 million.
Learn more about the CABLE Conductor Manufacturing Prize, follow the prize for updates on Stage 3, and explore NREL's research and development in advanced manufacturing.
Last Updated May 28, 2025