Invertible Neural Network Tool Helps Optimize Airfoil Design
Humans have always developed tools or technologies to help us surmount challenges. Obstacles encourage people to innovate.
The airfoil design problem—where an engineer works to build a shape with desired characteristics, such as maximizing lift while minimizing drag—presents an opportunity for innovation. Researchers at the National Renewable Energy Laboratory (NREL) are building computational tools using artificial intelligence (AI) that can help optimize airfoil design for wind turbine blades, aircraft wings, and fan blades in natural gas turbines.
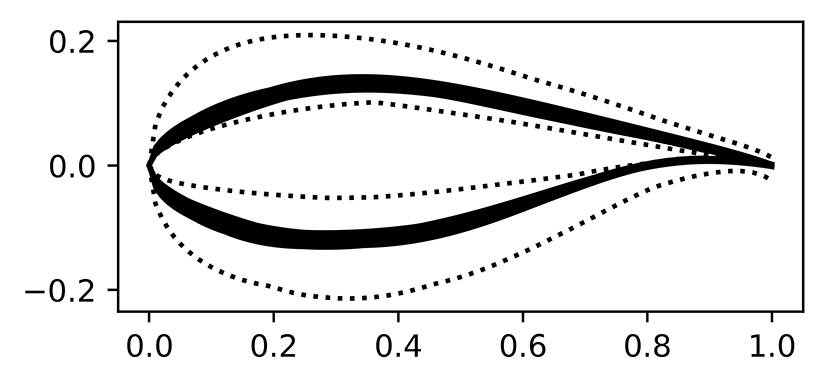
“Wind turbine airfoil and blade design is a complex, interdisciplinary process that must balance a wide range of objectives in the shifting landscape of customer demands, policy regulations, and technological innovations,” said Andrew Glaws, an NREL computational science researcher working to pave the way for improved airfoil designs. “Further, design iterations must move extremely quickly to keep pace with the market. To achieve all of this, designers use cheap, low-fidelity tools to rapidly create and assess new designs. Our work seeks to inject higher fidelity insights (e.g., nonlinear aerodynamic effects) into the design process without affecting their tight timelines.”
Higher-fidelity means greater confidence in results—there is always some error in modeling. Low-fidelity models are fast to reduce the number of design iterations that require high-fidelity refinement, and researchers know that they only give an indication of how the airfoil will perform. Starting with more accurate inputs means researchers can further narrow the number of designs that need additional high-fidelity modeling.
The airfoil design process can be described as one of setting desired properties and characteristics and reverse-engineering the airfoil using an optimization method to reach that solution. Traditional optimization methods, however, are expensive, and they necessitate many evaluations of a model as researchers optimize a single airfoil. Such techniques may increase computing storage requirements, reduce the computational savings, or require repeated airfoil shape optimizations.
Researchers are exploring deep-learning models using neural networks to accelerate the design process. These networks perform well on human-oriented tasks such as natural language processing to decision making—additionally, they may potentially help identify optimized airfoil shapes.
INNs May Open Path Forward to Optimized Airfoil Design
NREL researchers have demonstrated promising methods for producing rapid airfoil shape designs for wind turbines using invertible neural network (INN) tools. The approach—recently detailed in AIAA Journal—demonstrates an approximately hundredfold speedup over current methods and satisfies the performance characteristics of airfoils used in wind turbine blades.
“The INN learns an invertible relationship between airfoil/blade shapes and their aerodynamic and structural properties, which allows designers to specify target performance characteristics and then rapidly explore the space of the shapes that correspond to those design targets,” said Glaws, lead author on the study. “The INN achieves this through the use of closed-form invertible blocks that are trained in a bidirectional manner that combines supervised (labeled) and unsupervised (unlabeled) loss functions.”

Glaws and team evaluated how various factors affect INN performance. They examined different INN model architectures to identify an optimal trade-off that balances the stability, performance, and training costs of the INN. They also evaluated unsupervised network training in generating plausible designs, network modifications to the baseline INN approach, and, most importantly, the performance of the proposed INN methodology in producing airfoil designs with the desired characteristics.
“We found that the INN was able to produce a range of unique airfoil shapes that correlated to various target performance characteristics within reasonable tolerance,” Glaws said. “However, we did find training the network to be a somewhat difficult balancing act between obtaining accurate forward predictions and ensuring reasonable inverse designs. A variety of other generative AI tools exist for performing similar design processes (e.g., GANs and VAEs), but these rely on multiple networks to learn the appropriate relationship. This can require more training data, slow the training process, and lead to large, memory-intensive models when compared to the shared weights of the INN.”
NREL has created open-source tools for the INN-based design framework and made them available at GitHub. The team also created an interface to use the INN within NREL’s WISDEM blade design framework. Glaws said that the team is eager for researchers and designers to access these tools, provide feedback, and help explore how the team can further improve upon them.
“We’re excited about the potential impact that the INN can provide as a generative AI approach to accelerate wind turbine design processes,” Glaws said. “Additionally, we are excited by the breadth of new research directions that this work has opened up, including questions about improved 2D/3D shape representations, robust design for blades experiencing erosion or icing, and the possibility of extending this work to the design of other components such as floating offshore platforms.”
Learn more about NREL’s machine learning research. And check out how NREL’s computational science tools help researchers answer energy questions.
Last Updated May 28, 2025