Industrialized Construction Innovation
NREL research delivers affordable, grid-efficient, net-zero energy buildings and components using innovative industrialized construction techniques.
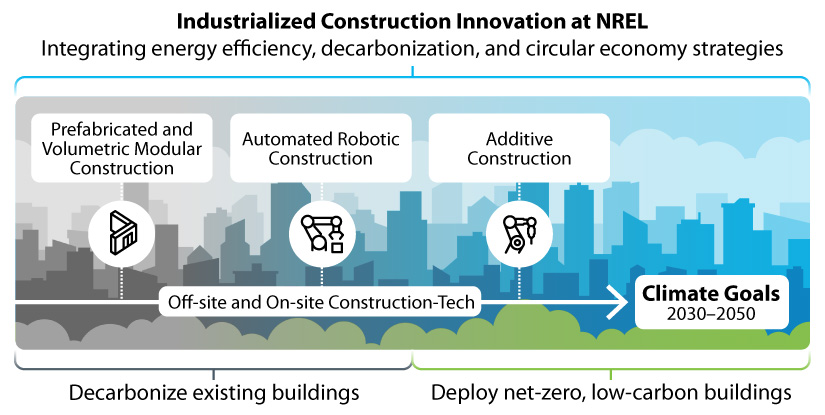
Industrialized construction uses industrialized production methods—such as high-volume off-site construction, prefabrication, and on-site construction automation—to build or retrofit buildings, leading to reduced costs and the potential for increased energy efficiency and decarbonization. In addition to reducing the cost of construction and delivery time, industrialized methods such as permanent modular construction have the potential to deliver affordable buildings at scale, building decarbonization, electrification strategies, grid friendliness, and resilience.
Capabilities
NREL can modernize off-site factories and retrofit/construction sites that produce industrialized construction products—such as panels, pods, and modular buildings—to address the affordable housing crisis by lowering construction costs, reducing the energy burden, and mitigating greenhouse gas emissions.
Research Block
Research Block is an outdoor pad at the NREL campus in Golden, Colorado, that allows apartment-in-the-loop research and development. Ongoing efforts include field testing of envelope thermal control, envelope infiltration control, and advanced smart and grid-interactive controls. NREL leverages two modular apartment units—iUnit and Blok—to perform a series of experiments.
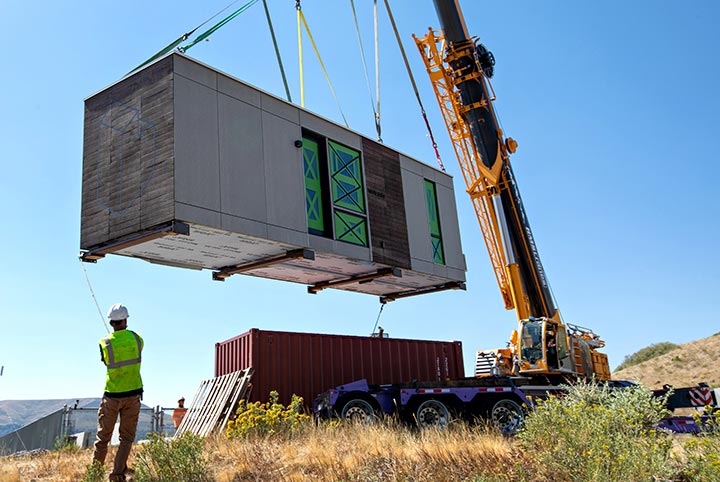
A Blok modular apartment unit is installed at the NREL Research Block.
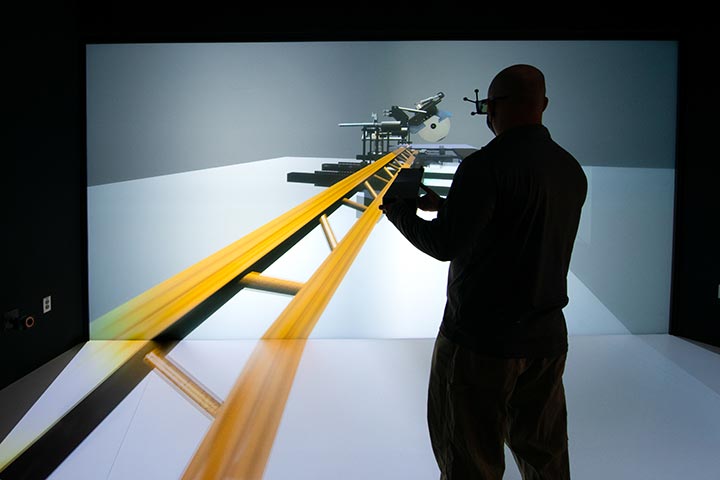
An NREL researcher pilots Immersive Industrialized Construction Environments in the Visualization Room at NREL’s Insight Center.
Immersive Industrialized Construction Environments
NREL is developing and testing Immersive Industrialized Construction Environments for construction automation and worker-machine interaction to investigate possible solutions to challenges with energy efficiency integration and workforce productivity.
Focus Areas
We aim to modernize the U.S. built environment with improved energy efficiency and reduced greenhouse gas emissions by bringing our expertise to industrialized construction partners.
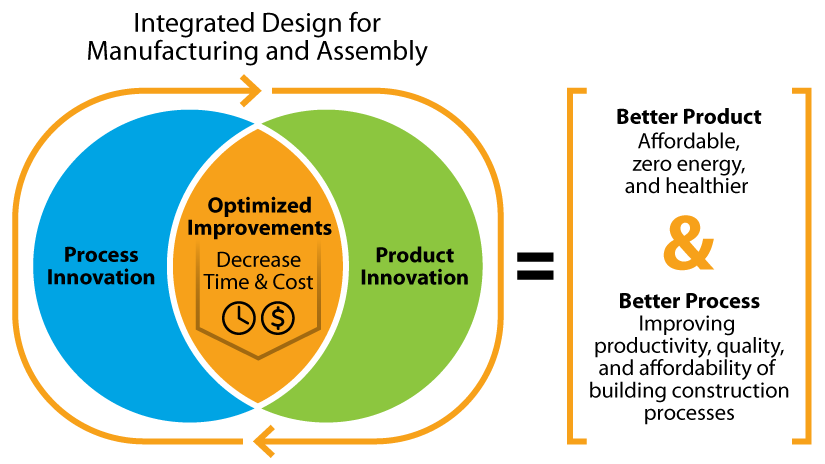
Process Simulation and Productivity Modeling
We work with teams operating factories, deploying new factories, or considering off-site/on-site automation to improve productivity and processes through simulation models using data from factory cameras and sensors. Learn more in the Cityscape article How Can Construction Process Simulation Modeling Aid the Integration of Lean Principles in the Factory-Built Housing Industry?
Design for Manufacturing and Assembly, Whole-Building Systems Integration
We leverage approaches such as design for manufacturing and assembly to bring together energy efficiency and low-carbon strategies for retrofit and new industrialized construction. Learn more in Development of Integrated Mechanical Pods.
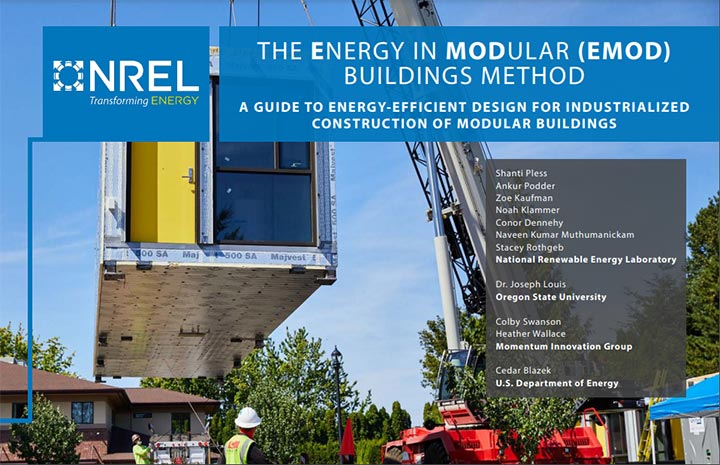
The Energy in Modular Buildings Method report provides a guide to NREL’s focus areas and approach to energy-efficient design for industrialized construction.
Building Energy Modeling and Moisture Management Modeling
An industrialized construction approach requires building energy design and modeling, including moisture management modeling, in the early prototyping stage to realize cost benefits (both upfront and operational).
Data Collection, Prototyping, and Field Pilots
We work with partners to develop pathways to assemble and integrate energy efficiency and low-carbon strategies on real-world production lines and in virtual reality using noninvasive construction and retrofit technologies tied to widely used process simulation modeling techniques, such as discrete event simulation modeling.
Integrated Workflows and Tool Development
Our approach involves streamlining workflows through integrated building product design and advanced manufacturing workflows. We introduce digitization and automation to support iterative product and process development cycles, streamlining workflows by using pre-run energy models and machine learning-based data analytics.
Circular Economy Pathways, Whole-Building Life Cycle Assessments, Scaling Decarbonization
We provide expertise on the circular economy, life cycle assessments, and developing decarbonization pathways to partners from all areas of industry. Circular economy and decarbonization pathways are a valuable resource in establishing corporate carbon-reduction goals. Learn more in Decarbonization During Predevelopment of Modular Building Solutions.
Partnerships and Projects
Multiple ongoing projects have been funded under DOE's Advanced Building Construction (ABC) Initiative. NREL's Industrialized Construction Innovation team works with partners such as Volumetric Building Companies (wood-framed volumetric modular builder), Factory_OS (steel-framed volumetric modular builder), and FullStack Modular (steel-framed volumetric modular builder) as well as other collaborators such as AeroBarrier Inc., VEIC, Solar Home Factory, STRATIS, KBS Builders, Denver Housing Agency, Group 14, Milender White, Stanford University's Center for Integrated Facility Engineering, Louisiana State University, Oregon State University, Module Housing (Last Mile Lab), Kit Switch, BLOX Inc., and Blokable Inc. in the United States.
Publications
A Scalable Method for Decarbonizing Modular Building Solutions, ACEEE Summer Study (2022)
Accelerating Optimal Integration of Energy Efficiency Strategies with Industrialized Modular Construction, ACEEE Summer Study (2022)
Contech to Accelerate Cleantech: Seeding Emerging Innovation Programs for Construction Productivity and Energy Efficiency Integration, ACEEE Summer Study (2022)
Industrialized and Robotic Construction Advances in Terrestrial Construction and Opportunities in Space Construction, NASA Marshall Space Flight Center Tech Talk (2022)
View all NREL publications about industrialized construction research.
Contact
Share
Last Updated Aug. 7, 2025