Modular Construction Enables Efficient and Affordable Housing
NREL Teams Up With iUnit To Advance Lower-Cost Modular Housing
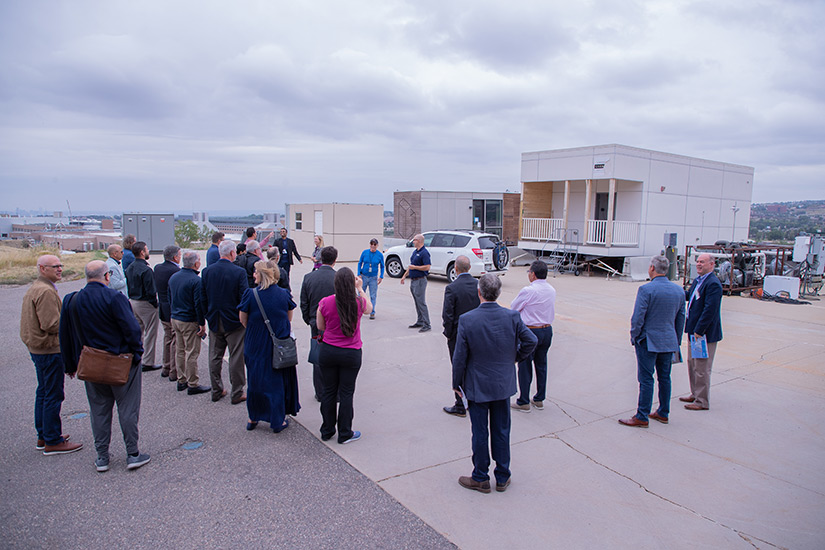
NREL researcher Shanti Pless (center) introduces visitors to the NREL Research Block, which currently hosts iUnit Communities’ modular apartment prototype, shown on the right. Photo by Joe DelNero, NREL
Recently, Shanti Pless stood on a windswept hillside and listed some of the issues that come with leaky envelopes. While that phrase may conjure surreal images of damp greeting cards, the National Renewable Energy Laboratory (NREL) researcher was actually explaining the problems that arise when too much air can escape a building through its walls, windows, doors, and other openings.
"You're paying money to heat and cool your space," Pless explained. "A leaky envelope allows conditioned inside air to escape and outdoor air to enter. This makes it harder to maintain a stable indoor temperature, which leads to less efficient buildings and increased utility bills."
To improve building efficiency, Pless and NREL's Industrialized Construction Innovation (ICI) team have partnered with Virginia housing developer iUnit Communities, using iUnit's modular apartment prototype as a testing ground. NREL hosts the 380-square-foot prototype, which features a supertight building envelope, high-performance heating, ventilating, and air conditioning (HVAC) system, and affordable appliances, on that windswept hillside on the laboratory's South Table Mountain Campus in Golden, Colorado. Here, researchers conduct field tests to measure the prototype's performance and efficiency. Through this research, the ICI team studies how methods like automation, factory construction, and prefabrication can deliver affordable, reliable, energy-efficient residential buildings—while enhancing the U.S. construction workforce.
Greater Performance, Lower Costs
The high costs of housing and energy are enough to keep many consumers up at night. Addressing these challenges requires innovative housing solutions that reduce costs and improve building performance.
"How do we create housing that is efficient and therefore truly affordable?" iUnit founder Brice Leconte asked.
That question inspired Leconte to found iUnit Communities, which develops and manages residential communities focused on smart living, energy efficiency, and modern design. iUnit's first apartment community, Eliot Flats in Denver, consists of 40 studio and one-bedroom units. Each unit was built in a factory and fully integrated with energy-efficient HVAC and water systems, as well as the capability to access hybrid energy sources, before being delivered to the Eliot Flats site and assembled into a three-story apartment building.
iUnit's approach is unique for several reasons: First, the iUnit community model can function as a microgrid, meaning the structures can be equipped to generate and store energy. This capability reduces reliance on the traditional grid, enhancing resilience against power outages and lowering energy costs for residents. Those energy-generating features are integrated into the unit when it is constructed in the factory, which means that each unit arrives on-site fully equipped and move-in ready.
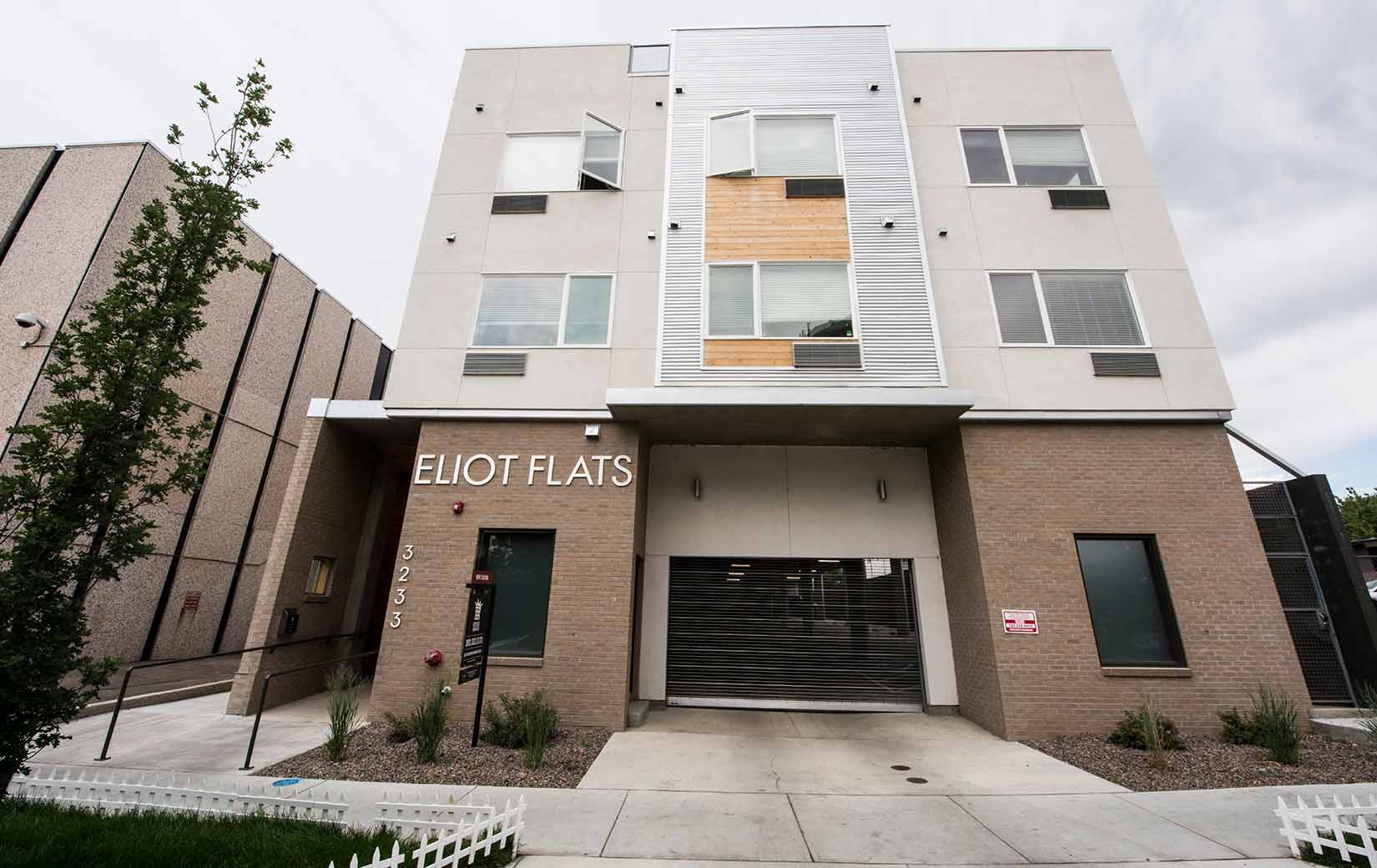
"Because we're working in a controlled environment, we can deliver a turnkey product," Leconte explained. "Much like a car rolls off the assembly line ready to drive, our homes are ready to use upon delivery."
Finally, building the units in the controlled environment of a factory allows iUnit to standardize its construction processes, improve quality control, and reduce costs—which makes the homes more affordable to renters.
"By integrating modular design and factory-built systems, we can streamline construction, maximize savings, and boost housing supply," said NREL researcher Nick Cindrich, who also works on the iUnit project. "This ensures more affordable, high-performance housing options for those who need them most."
NREL and iUnit Join Forces
Around the same time iUnit built the Eliot Flats community, Leconte connected with Shanti Pless at a conference, and the two decided to join forces to use an iUnit studio as a testing ground for cost-effective, modular construction methods and energy-efficient housing. Leconte agreed to provide the studio—the same as those at Eliot Flats—and Pless and the ICI team agreed to conduct the research.
The iUnit prototype arrived at the South Table Mountain Campus in 2017 and was housed in NREL's Energy Systems Integration Facility (ESIF), where the ICI team studied the efficiency of the unit's integrated heat pump system and advanced smart and grid-interactive controls. iUnit incorporated lessons from this research into production of newer studios. In 2019, the team moved the prototype out of the climate-controlled environment of ESIF to the campus's Research Block. At this new location, the team has been performing field tests to understand how real-world conditions impact the prototype's energy performance.
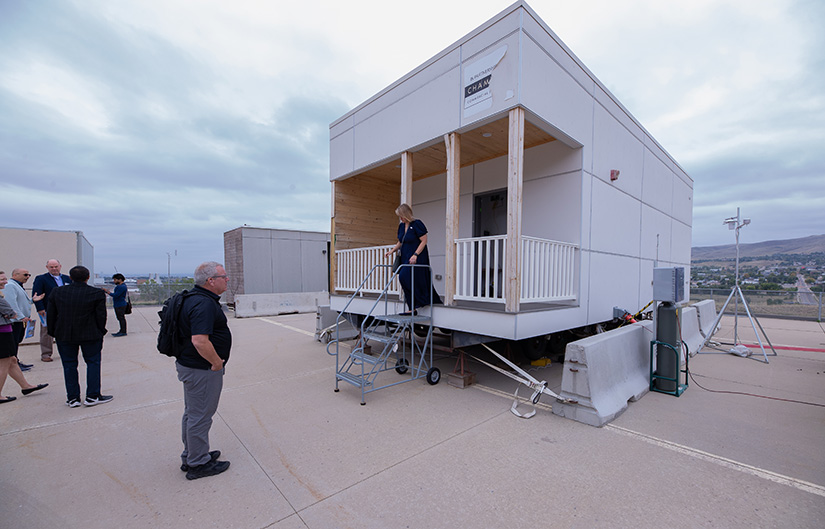
Most recently, the team investigated the iUnit prototype's air infiltration and thermal performance—technical terms for determining the leakiness of a building envelope. Over the course of a year, the team pumped carbon dioxide (CO2) into the unit and used sensors to measure the CO2's decay, or how much the CO2 decreased, which indicated how much outside air leaked into the unit under varying weather conditions.
"If CO2 levels drop quickly, it means lots of outside air is entering and indoor air is escaping, indicating a leaky building envelope," Pless explained. "If the level drops slowly, the space is more airtight, with less unwanted airflow. Data like this will give us valuable insights into how to optimize air barriers and improve our energy modeling tools."
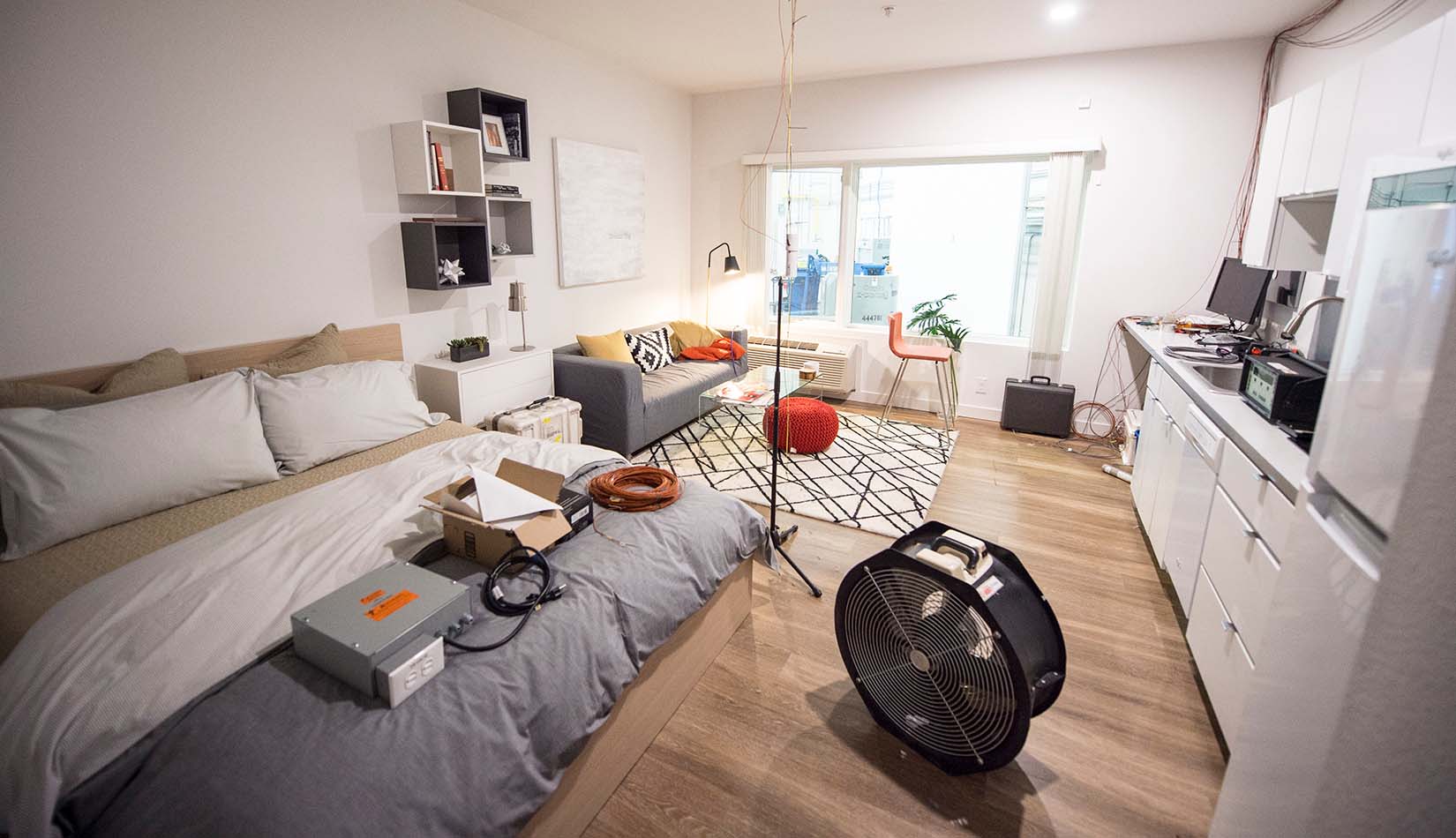
The ICI team uses the results of field experiments like these to help developers and factories adopt energy-efficient modular construction practices. These methods help improve energy efficiency, lower construction costs, and expand access to high-performance, affordable homes nationwide.
NREL is also developing and testing virtual construction training and testing spaces called Immersive Industrialized Construction Environments, in which workers and machines collaborate to make construction faster, safer, and more productive. By training workers in this immersive environment, the program makes learning about automation and energy-efficient construction more accessible, scalable, and safer.
A Win for Workers, Property Owners, and Residents
In addition to enhancing energy efficiency and affordability, industrialized construction has the potential to transform the construction workforce. By creating jobs in a factory setting, industrialized construction offers workers safe working conditions and new career options in a rapidly evolving industry. Factory-built construction offers a solution: Instead of battling the elements on a construction site, workers carry out their tasks in a controlled setting. That controlled setting facilitates standardized processes, enabling employers to offer training in advanced building technologies.
"iUnit exemplifies this approach by designing housing units that are fully equipped with heating, cooling, and energy systems before they leave the factory," Pless said. "This not only streamlines construction; it creates demand for a skilled workforce trained in energy-efficient building, automation, and smart home technology. It's a win-win."
Visit our Industrialized Construction Innovation page to learn more about NREL's research.
Last Updated May 28, 2025