Short-Circuiting on Purpose: How NREL-Licensed Tech Continues To Make a Difference in Space
Before sending any piece of equipment into space, NASA tries to limit and plan for any failure with exhaustive testing—down to the individual cells inside a battery.
To do that well, NASA and the National Renewable Energy Laboratory (NREL) created a device that causes an internal short circuit inside the layers of a battery cell, intentionally corrupting the cell by melting a thin layer of wax and forcing test cells to fail at a precise time and location within the cell. This information allows NASA to meet its stringent battery safety requirements.
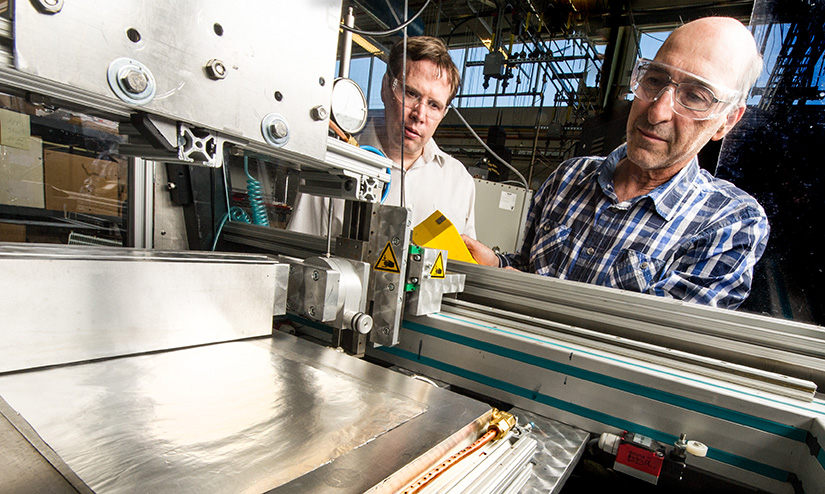
“If you know how the cell is going to respond with an internal short circuit, you can come up with ways to make that cell safer,” said NREL’s Matt Keyser, senior energy storage engineer. “Once you understand how it fails, then you can look at what’s available to address the point of failure.”
This is essential for testing batteries in the International Space Station, the Artemis missions to the moon, and future missions to Mars.
“The internal short circuit device (ISC-D) trigger cells are our preferred method of conducting our battery test campaigns for all our manned missions,” said Eric Darcy, battery technical discipline lead at NASA’s Johnson Space Center.
Keyser, a 31-year NREL veteran, was part of the team that originally created the ISC-D, along with NREL’s Chief Energy Storage Engineer Ahmad Pesaran and NASA Engineer Eric Darcy.
“Back in 2010, I was awarded a sabbatical from NASA to work at NREL for a year,” Darcy said. “I was in Golden, Colorado, with Matt Keyser inventing the internal short circuit device. It barely worked, but we did a proof of concept during that year. By 2014, we finally had it ready for prime time.”
The device is implanted into the cell by the manufacturer, in between anode and cathode to become a special trigger cell with an on-demand internal short-circuit point. Once the insulating wax is melted, a hard short circuit results in the cell, responding as if it had a single point manufacturing-defect-induced internal short circuit.
Such defects still plague the lithium-ion cell industry and lead to rare but catastrophic field failures in batteries. The ISC-D method is more representative of these field failures than the standard nail-penetration method and can cause multiple internal shorts in the cell or heat triggers that melt large portions of the separator between anode and cathode above 130 degrees Celsius.
“We’d gone through all the iterations for the device, but it wasn’t quite right,” Keyser said. “When Eric started his sabbatical, he suggested trying paraffin wax as an insulator.”
The paraffin wax turned out to be too brittle, so Keyser investigated microcrystalline wax, which was too soft. The Goldilocks wax was a combination of paraffin and microcrystalline. The wax also has a melting point of 57 degrees Celsius, which is much lower than other forms of testing.
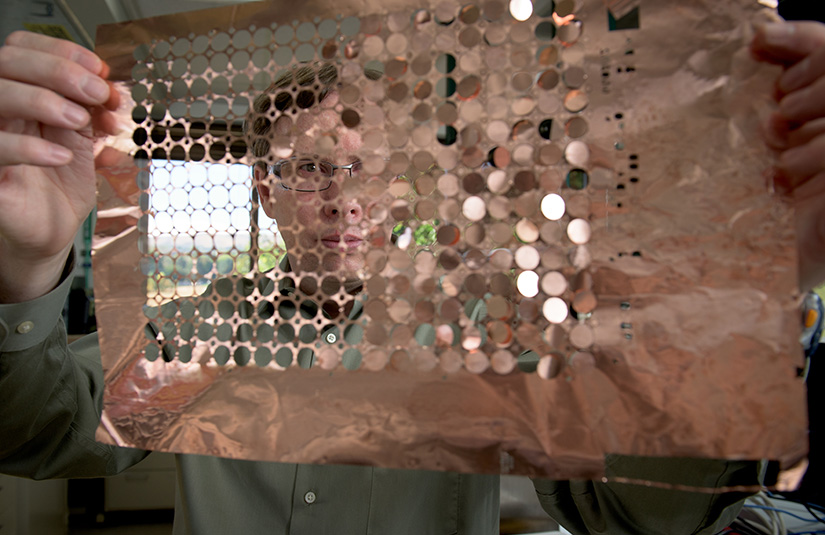
“Nearly all battery designs for manned spacecraft applications have been verified to resist propagation of thermal runaway from cell to cell thanks to test campaigns using trigger cells with the ISC-D,” Darcy said. “This method ensures the least risk of overtesting or undertesting when instigating an individual cell thermal runaway (TR) event in a battery with many cells. Properly designed batteries can tolerate a single-cell TR event in any location without propagation, which only degrades performance. In contrast, if TR propagation from cell to cell occurs, it can mean a catastrophic failure. It can take down the capsule, with loss of vehicle and/or loss of crew.”
Technology Licensing Enables Full-Scale Commercialization
After the team got the ISC-D to work consistently such that large test batteries could be assembled with these trigger cells, the technology earned an R&D 100 award, and NREL began talks with a company called KULR Technology Group about licensing the technology from NREL. NREL licenses its technologies to companies through the Technology Transfer Office, because the laboratory prioritizes research over mass production.
“It’s not something researchers are ready for—to make hundreds of devices in the exact same fashion over and over again,” Keyser said. “We research new inventions and, if it works, transfer to industry and progress to the next project.”
NREL granted KULR an exclusive license in 2018, and the company now sells the ISC-D to a variety of battery manufacturers, including those that supply NASA, meaning the technology has come full circle.
“At KULR we focus on all things battery-safety related,” KULR Chief Technology Officer and past NASA battery engineer Will Walker said.
What does it mean to design a safe battery and to demonstrate safety in the form of a test?
“There’s significant difficulty in pack- and system-level thermal runaway testing,” Walker said. “The beauty of the ISC-D cell is that it triggers at a lower controlled temperature, resulting in less biasing on neighboring cells in the experiment. The result is a less-invasive triggering method as a whole.”
With the licensing agreement, KULR has the exclusive rights to sell the ISC-D and cells that have the ISC-D implanted.
“It is a very elegant solution,” Walker said. “For KULR, we want to be on the forefront of cutting-edge technology as it pertains to safety, and this is the only true noninvasive triggering method available.”
The batteries NASA is testing with the ISC-D include those in new astronaut suits, equipment, and human-rated spacecraft.
Recently, a university group came to NREL to present the best ways to test an internal battery cell. Keyser was in the audience when the group concluded that the NREL team’s ISC-D technology is the best.
“That was very satisfying for me,” Keyser said. “The technology we’ve developed is the best technology to simulate an internal short circuit.”
The ISC-D can be used to test electric vehicle or grid batteries as well. Keyser also hopes several testing organizations will adopt the technology as part of their processes.
“There are a number of manufacturers that use this, but I want to see it incorporated into testing procedures and protocols in order to make cells safer,” Keyser said. “Our technology is the only one that can mimic a true internal short circuit, giving battery engineers an accurate picture so they can design safer battery systems.”
Learn more about NREL's energy storage research and sustainable transportation and mobility research. And sign up for NREL's quarterly transportation and mobility research newsletter, Sustainable Mobility Matters, to stay current on the latest news.
Last Updated May 28, 2025