Winners of Geothermal Manufacturing Prize Dig Deep--and Take Home $500K
Winning Teams 3D Print Their Way to Victory
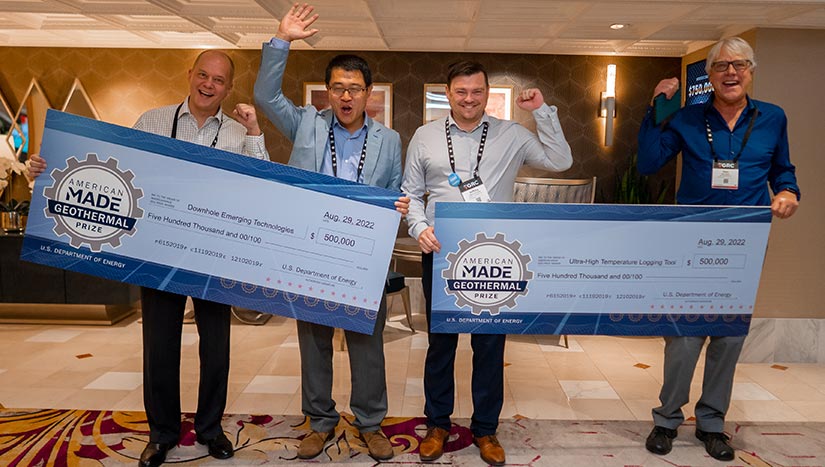
After successful presentations at Geo! Demo Day, the concluding event of the American-Made Geothermal Manufacturing Prize, two teams were named winners and awarded $500,000 each. The teams, Downhole Emerging Technologies and Ultra-High Temperature Logging Tool, used additive manufacturing (i.e., 3D printing) to solve common challenges unique to the geothermal energy field.
During the final Geo! Contest, competing teams were required to present their manufactured functional prototype, with all additive manufacturing components incorporated and tested, to a panel of expert reviewers. The winner announcement was made during the plenary session of the Geothermal Rising Conference on August 29 in Reno, Nevada. The teams also earned up to $200,000 each in reimbursements for field testing costs.
"Winning this Geo! Contest is what's going to allow us to improve the design, finish the testing, and get to the field," said Jeff Johnston from Ultra-High Temperature Logging Tool (UHTLT).
"Our end game is to get the tool in the ground within the year and hopefully turn it into a viable product that can generate revenue," said Justin Scruggs, also from UHTLT. "But regardless of whether that happens, just doing the contest and making contacts has been an incredible experience."
About the Prize
The American-Made Geothermal Manufacturing Prize was designed to inspire innovative concepts that use additive manufacturing to address the challenges fundamental to operating in harsh geothermal environments.
These harsh environments require manufacturing tools, components, and equipment that can handle the heat (literally!) and still be able to drill through hard rock and withstand corrosive fluids. Tools and equipment must consequently be made with high-grade materials and specialized geometries that are expensive to manufacture—especially given the small size of the U.S. geothermal market. Because of the rough conditions under which they perform, the tools also have pretty short life spans.
Enter additive manufacturing, a way to produce the tools needed for geothermal drilling's unique requirements that is often more cost effective and offers huge potential for innovation. The Geothermal Manufacturing Prize was created to encourage engineers and entrepreneurs to take advantage of 3D printing's capabilities to enhance some of these specialized tools.
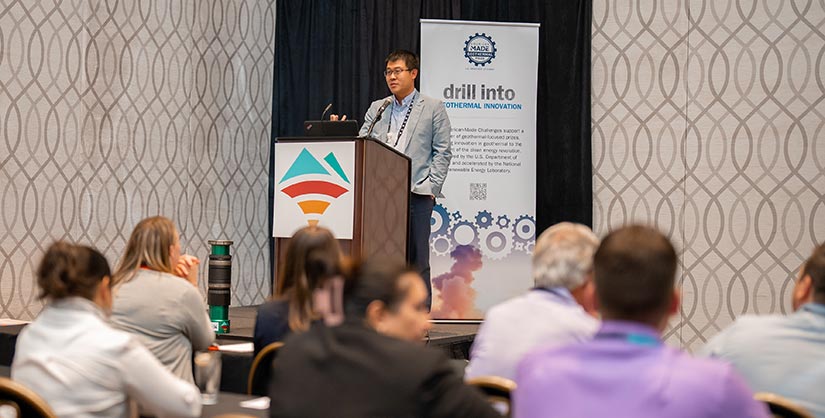
For Downhole Emerging Technologies (DET), incorporating additive manufacturing into the prototype they had already developed—prior to the competition—was a game changer. Their metal zonal isolation packer, a cylinder that can be crushed to fit into the well, expanded to form a "plug," then crushed again for removal, was originally just made of machined metal.
"We looked at how additive manufacturing could change the design of this thing to make it better," said Ken Havlinek of DET, who "stumbled upon" a 3D-printing solution. Now, he said, their prototype would not function without the additively manufactured alloy components that anchor the packer in its hole. "There's no other way of making this thing," he said.
Figuring Out Where To Begin
DET knew that there was a need for innovations around packers made specifically for the geothermal industry before they began creating their concept. (Havlinek noted that these types of packer plugs are also used in oil and gas wells but are usually made of rubber, which are unable to withstand the high heat of geothermal wells.)
UHTLT took a crowdsourcing approach when they began their innovation journey.
"We knew that we wanted to do something unique and disruptive with additive manufacturing," Johnston said, adding that they did not go into the challenge knowing they were going to develop a logging tool. "We asked the industry what was missing, what would make their lives easier, and a recurring theme was ‘we need logging tools that last longer downhole.'"
So, the team got to work figuring out a way to use additive manufacturing to protect temperature-sensitive electronics.
"We created a next-generation tool that can actually monitor pressure, temperature, flow rate, etc., down in the well," UHTLT's Christopher Taylor said. "But because it is very hot and the conditions are very corrosive, the tool has to be well designed to collect enough data. We used additive manufacturing to create a geometry for protecting the sensitive electronics inside the tool from those extreme environments."
Ready, Set, Make, Geo!
Prior to their big win, both teams had already won the Ready!, Set!, and Make! Contests of the prize, winning cash awards and support vouchers at each stage. That funding, the vouchers, and the notoriety that came with winning each stage were helpful in getting the two winning teams to this point.
"As we moved through the phases and more funding and more vouchers became available, we were able to mature the technology," UHTLT's Johnston said.
UHTLT's team also took full advantage of the voucher system, which they cashed in at Sandia and Oak Ridge National Laboratories. The vouchers, Johnston said, "gave us the ability to get in and work with these national labs, where otherwise we would not have been able to do that."
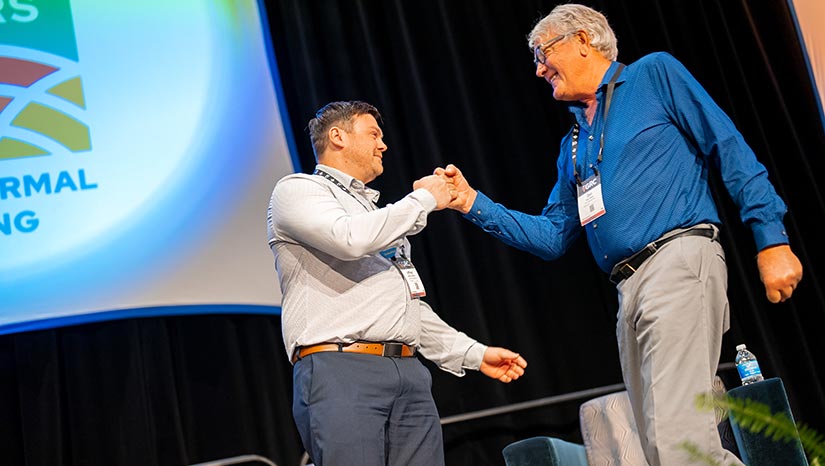
"Without this challenge, this technology wouldn't exist," Johnston said, adding that they are already making plans for revisions, retests at Sandia, and hopefully, some successful field tests. "What I would really like to see is our team come to the Geothermal Rising Conference next year and present a paper on the results of our field tests."
For DET, winning each successive contest has been beneficial not just in terms of cash flow, but also in terms of industry recognition.
"It's really nice to have others recognize that this is an interesting and valuable invention and put money into it to help us get to the finish line," Havlinek said.
Prize administrators hope that the innovations that result from the competition will help support the geothermal industry's ability to reach the target of 60 GWe of geothermal capacity by 2050, as outlined in the GeoVision analysis performed by the U.S. Department of Energy's Geothermal Technologies Office.
The American-Made Geothermal Manufacturing Prize is supported by the Geothermal Technologies Office and the Advanced Manufacturing Office in the U.S. Department of Energy's Office of Energy Efficiency and Renewable Energy, in partnership with the National Renewable Energy Laboratory and Oak Ridge National Laboratory.
Last Updated May 28, 2025