Considerations To Achieve a Sustainable U.S. Commercial Building Stock
New Study Led by the Joint Institute for Strategic Energy Analysis Identifies Drivers, Barriers, and Costs of Adopting Building Sensors and Controls Systems
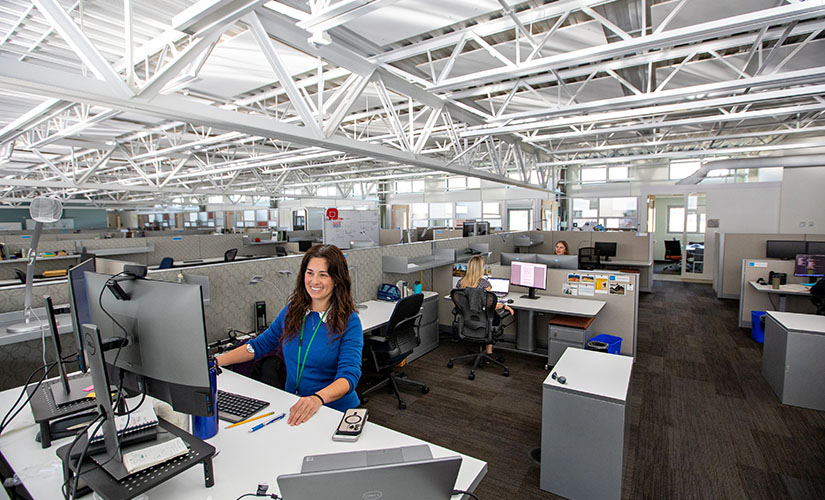
Building sensors and controls systems are automated controls systems that can regulate a building's heating, ventilation, and air conditioning (HVAC), lighting, appliances, and more to increase energy efficiency. These systems can save building owners money, enable buildings to be grid-interactive, and support decarbonization.
Nearly 60% of U.S. commercial buildings over 50,000 square feet have sensors and controls systems, but only 13% of buildings under 50,000 square feet have the technology—meaning more than 75% of the U.S. commercial building stock has untapped efficiency potential.
The Joint Institute for Strategic Energy Analysis (JISEA) studied barriers and drivers of adopting building sensors and controls systems and created a full breakdown of costs. This work, which was done in partnership with the National Renewable Energy Laboratory (NREL), falls under JISEA's Clean Energy Manufacturing Analysis Center. The findings are published in a JISEA technical report.
"The technologies exist for the buildings sector to be more energy efficient and sustainable, but high market adoption is complicated," said Kim Trenbath, NREL researcher and lead author. "Our insights highlight the major considerations building owners take into account when deciding whether to adopt a sensors and controls system, so we can better understand what it will take to achieve widespread adoption."
Drivers and Barriers to Adoption
Based on interviews with building owners, contractors, controls vendors, analytics vendors, and researchers, JISEA finds that the biggest driver to adopting a building sensors and controls system is the operational benefits and insights. Building owners like that the technology allows them to automate building schedules, seasonal changes, and more, and that they don't have to call technicians as often. Building owners can also tap into operational insights such as energy consumption or occupancy patterns.
While the operational benefits garner interest among building owners, JISEA finds three key barriers to adopting a building sensors and controls system: (1) The systems can be confusing and/or complex, (2) owners do not have the skills or expertise to use the system, and (3) owners cannot justify the upfront cost.
"We find that the upfront cost and difficulty quantifying savings lead to a perception that these systems aren't profitable," said Ryan Meyer, NREL researcher and co-author. "But studies have shown widespread adoption could reduce energy costs by 29% across the commercial building sector."
To enhance system interoperability and usability, JISEA recommends consistency and standardization across controls technologies to support greater adoption, especially for buildings that historically have not implemented these technologies.
System Cost Breakdown
Knowing cost can be a barrier to adoption, JISEA created a complete cost breakdown for multiple building sensors and controls systems. Data came from several sources, such as project invoices and estimates and available cost information from various manufacturers.
Based on the data, JISEA finds 50%–75% of the cost of a building sensors and controls system comes from labor. Because the systems are complex, they require specialized labor. It is no longer sufficient for an installer to have the skills for even the most advanced HVAC systems because the new technology specifications require a more IT-focused skillset. The specialized labor results in higher costs. Labor rates and contractor pricing/markup vary regionally and can significantly impact overall cost. For example, a project that costs $780,000 in Dallas could cost upward of $1.8 million in New York City.
"There could be ways to allow equipment-embedded controllers to connect wirelessly and interoperate with the central control system, similar to how edge computing networks are operated, so there is less hardware, which would also reduce labor cost," Trenbath said. "These are the types of possible solutions that will be important to study moving forward to help remove barriers to adoption."
Learn More
Read the full JISEA technical report or get the high-level findings in a JISEA research highlight. Learn more about NREL's buildings research.
Note: The Joint Institute for Strategic Energy Analysis retired in February 2025.
Last Updated May 28, 2025