Powering the Next Wave of Energy Converter Devices
NREL completes multiyear system design and validation project with Columbia Power using the 5-megawatt dynamometer.
A multiyear system design and validation project funded by the U.S. Department of Energy Water Power Technologies Office reached completion in 2019 and resulted in increased knowledge about development and validation of wave energy converter devices and their associated materials.
The project demonstrated the feasibility of safely conducting low-speed reciprocating trials of wave energy converter systems using a traditional wind turbine dynamometer by putting Columbia Power’s power-take-off module (PTO), LandRAY, through its paces in the 5-megawatt dynamometer facility at the National Renewable Energy Laboratory’s (NREL’s) Flatirons Campus.
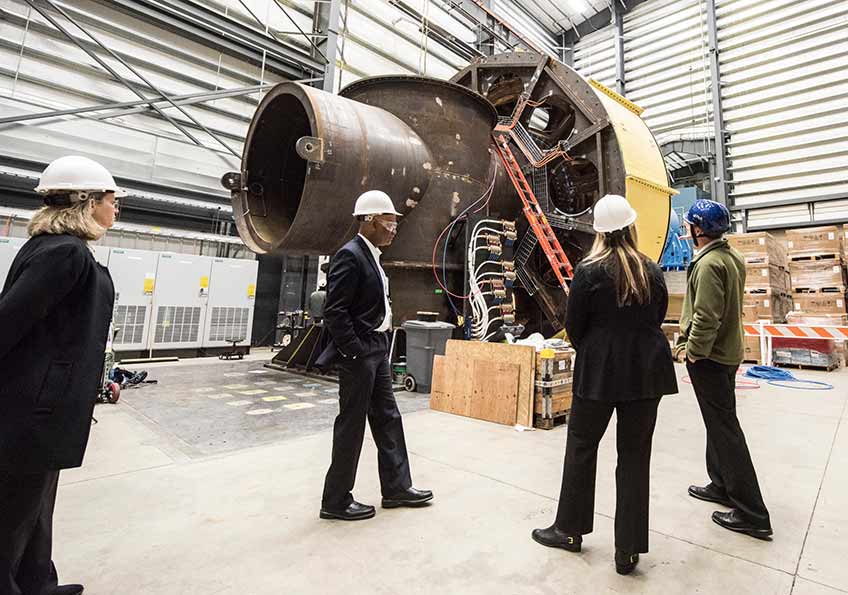
Validation of LandRAY at the Flatirons Campus provided an opportunity to simulate open-ocean operating conditions with an economical land-based assessment. The PTO module is key to delivering cost-competitive wave energy, and basically functions as the generator. The project covered 12 stages of design, assembly, and validation engineered to thoroughly characterize the PTO components by using overlapping data sets to isolate assessment results.
Structural validation capabilities at NREL’s Flatirons campus provided Columbia Power the opportunity to validate over 150 composite coupons, fabricate 85 metal and adhesive double lap shear component specimens, and validate double lap shear components with over 38 million fatigue cycles, providing further analysis and data to Columbia Power.
The emerging marine and hydrokinetic power industry benefits from this effort in several ways. The performance of the novel low-speed generator demonstrated the feasibility of the segmented design for large-diameter direct-drive applications by showing a 40% airgap reduction, with further analysis showing that additional reductions are possible. These airgap reductions minimize the amount of electrical energy needed to create the magnetic field of the motor, improving motor energy output and efficiency. The verification, validation, and data-analysis steps increased the body of knowledge of direct-drive permanent-magnet generators, which are important for the continued development of the marine and hydrokinetic power industry.
Learn more about NREL’s Dynamometer Research Facilities and Structural Research Capabilities.
Last Updated May 28, 2025