Advanced Wells
NREL and its partners are reinventing the future of geothermal drilling and advanced wells.
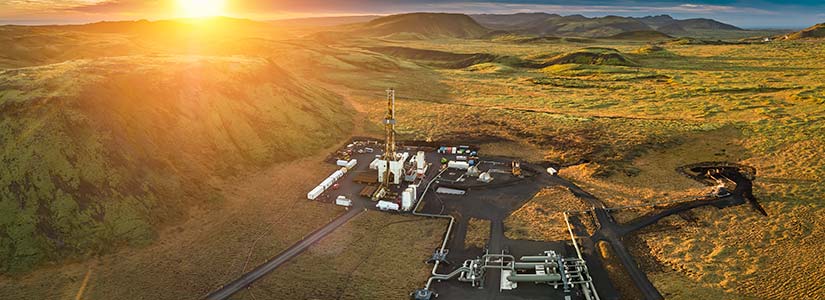
Drilling, constructing, and operating wells in harsh geothermal environments requires advanced techniques and technologies relative to drilling for water or oil and gas. As developers target deeper and hotter resources—as well as elaborate well designs—technologies and efficiency also need to improve.
High-Temperature, High-Pressure Tools
Downhole drilling tools significantly improve the accuracy of data. Surface measurements are impaired by boundary effects because of torque and drag alongside the drill string, torsional drill-string wrapping, and drilling dysfunctions. These effects make it challenging to discern true downhole bit conditions. Downhole data collection in the oil and gas industry has decreased drilling time and costs while increasing penetration rates by 35%–55%. NREL scientists are using new materials and designs to increase the temperature and pressure capability of these tools for use in high-temperature (>250°C) geothermal wells.
Innovative Drilling Systems
NREL researchers are working to advance high-temperature/hard-rock geothermal drilling. Rotary drilling has been used to drill wells of all types for more than a century. Over this time, advances have led to faster drilling rates, which have increasingly allowed for economic access to oil and gas plays throughout the world. However, geothermal heat is often found in harder, hotter, and potentially deeper rock. Although recent drilling projects in Utah and California have recorded significant improvements in rates of penetration and bit life, there are still vast opportunities to improve drilling performance and efficiency through improved bit design, novel drilling methods, and data-informed operations.
Well Construction Materials
NREL is using its expertise in ceramics, metallurgy, and polymer development to advance well construction materials and designs.
Unlike short-lived oil and gas wells, geothermal wells must last decades under constant use, harsh conditions, and thermal cycling. The higher the well temperature, the more economically attractive the geothermal well is. It is therefore important that the geothermal industry develop well materials (both casing and cement backing) that can survive for years in harsh geothermal environments. NREL works with partners on well construction materials capable of withstanding very high geothermal temperatures (>300°C), pressures and and salinities.
Geothermal Energy From Oil and Gas Wells
NREL experts are working to use renewable resources in combination with fossil energy. Geothermal and oil and gas hybrid systems make use of wells already drilled by oil and gas developers, creating synergies in these related industries. Coproducing energy from oil and gas reservoirs producing large amounts of hot water is considered for some projects. Using geothermal fluids from these wells for energy production (i.e., direct-use heating or electricity) can extend the economic life of existing wells, deliver near-term energy savings, and reduce greenhouse gas emissions.
Featured Projects
In the RePED 250 project, NREL researchers are working to adapt Tetra Innovation Institute's patented pulsed power drilling technology to the hotter, harder, crystalline rock found in geothermal wells using high-temperature power electronics, including alternators, capacitors, and high-voltage, pulsed-power switches. If successful, the technology is expected to disrupt the global drilling industry and replace traditional drilling technologies within 10 years of commercialization.
Competitive market modeling shows the potential for an additional 50 GW of geothermal deployed in the United States because of cost and time improvements from this technology. High-temperature power electronics developed through this research will also have immediate applicability to industries including petroleum, aviation, fuel cells, vehicles, smart grid, and the military.
Impact
This technology would increase drilling rates tenfold, reduce geothermal well drilling costs by 75%, and cut development timelines, significantly increasing the market competitiveness of geothermal power.
Partners
Tetra Innovation Institute, TPL Inc., and the University of New Mexico
NREL is developing a new generation of electronics for harsh environments and specifically focusing on sensors, interface electronics, and packaging for downhole applications. Gallium oxide-based electronics have the potential for very high-temperature operation, so initial work has focused on developing sensors for downhole applications. To accomplish this also requires the development and qualification of new high-temperature contact metallurgies and robust packaging. We are investigating new inorganic and polymer composite encapsulants for both the sensor packages and downhole casing applications.
The objectives of NREL's materials for harsh geothermal environments effort are to:
- Develop next-generation sensors and power electronics based on gallium oxide and other functional oxides
- Develop thermodynamically and mechanically stable contacts for harsh environments
- Develop packaging for downhole environments based on novel tunable composites
- Validate the performance of new packaged electronics in downhole conditions
- Develop new approaches to stabilizing well casings for significantly longer downhole lifetimes.
Impact
Increased downhole sensor temperature limits facilitate geothermal drilling efficiency by incorporating NREL's aluminum gallium nitride materials in high-temperature sensing electronics.
Partners
National Oilwell Varco
Capabilities
NREL works with industry partners to design cost-effective drilling technologies that will enable the deployment of deeper and hotter geothermal across the United States. NREL's geothermal capabilities run the gamut from analysis to downhole tools/sensors and from reservoir modeling to full-scale field research validation. NREL also works with industry partners to evaluate the feasibility of using existing oil and gas wells for geothermal energy or storage applications. Learn more about these advanced wells capabilities:
Using its expertise in drilling and lean practices, NREL partners with industry to identify ways to reduce drilling costs by as much as 50%.
Declining oil prices in the late 1990s led to investments in drilling in an attempt to increase efficiency and decrease costs. The effort, which applied the principles of lean manufacturing to drilling, was successfully implemented by the onshore petroleum industry in the U.S. with a focus on standardization, optimization, and automation. The application of lean methodology to drilling realized cost savings of up to 50% and time savings of 15%–70%—even in hard-rock areas.
The largest savings have come from lean drilling processes, which can incur up to twice the planning man-hours of a traditional process. Successfully implementing lean methodology to the drilling process requires a significant change in mindset as well as the full support of all levels of a company, including managers, drilling contractors, operators, subsurface personnel, and drilling engineers.
NREL is working with geothermal operators to bring lean processes to the geothermal drilling industry. Time and experience have shown that significant savings are possible. If widely implemented, these savings could significantly increase profit margins and spark significant growth in the global geothermal industry.
Publications
Geothermal Drilling and Completions: Petroleum Practices Technology Transfer, NREL Technical Report (2018)
Geothermal Drilling: A Baseline Study of Nonproductive Time Related to Lost Circulation, 42nd Workshop on Geothermal Reservoir Engineering (2017)
Completion Design Considerations for a Horizontal Enhanced Geothermal System, Transactions (2015)
Contact
Dayo Akindipe
[email protected]
From new materials to new form figures, from packaging to reliability and validation, we are expanding capabilities for high-temperature power and sensing electronics.

Geothermal drilling is plagued by nonproductive time related to lost circulation, drill bit trips, and inefficiencies due to low rates of penetration and damaging drilling dynamics. Drilling time can be reduced by 50% by optimizing geothermal drilling through new sensing and electronics technologies. Downhole, high-temperature, and extended-range sensing downhole sensors can measure position, vibration, weight on bit, rotational speeds, and rock mechanics to facilitate drilling with higher efficiency, more reliability, and more range. Current downhole sensor technology is not reliable over 150°C, while anticipated drilling environments for geothermal surpass 400°C. The key to realizing lower drilling costs is the development of robust sensor packages that are survivable and provide data to improve efficiency.
NREL's research covers all aspects of sensor and power/signal electronics, including materials, contact metallurgies, and packaging. These components integrate to provide a downhole electronic platform capable of withstanding temperature, mechanical, and chemical stressors.
Patents
High Temperature and High Pressure AlGaN/GaN Electronics
Composite Packaging for Extreme Environments
Publications
Stable Contact Development for High-Temperature β-Ga2O3 Device Operation, APS March Meeting (2023)
Development of a 250 Degree C 15kV Supercascode Switch Using SiC JFET Technology, 2022 IEEE 9th Workshop on Wide Bandgap Power Devices & Applications (2022)
Contact
NREL's material science expertise spans the energy spectrum, allowing our scientists to leverage learning across industries.
Novel Cements

In the field of ceramics, our researchers have developed novel cements that emulate the durable ancient Roman cements of two millennia ago. These cements leverage the high temperatures of the subsurface (and some unique feedstocks) to form crystalline products that behave as a robust matrix with low permeability. The combination of low permeability, thermal resilience, and resistance to chemical attack indicate that this new (old) class of material may be integral in the future of geothermal cementing.
Casing Materials

Metal casing material is important for ensuring leak-free, constant geothermal production with no impact to shallow groundwater sources. NREL has developed processes to harden mild steel, which will limit the impacts of abrasion. In typical mild steel, scratches can act as a nucleating point for corrosive processes, so limiting abrasion is important for extending the life of inexpensive metal components downhole.
Also important to extending casing lifetime is limiting the steel's exposure to working fluid. NREL researchers are developing novel polymer-oxide composite materials that are extremely chemically stable and effective even above 350°C. The goal is to coat steel components with the chemically resistant composites to make casings that have the strength and cost of steel with the inertness of state-of-the-art alloys. Coupling robust cement backing with hardened and encased steel casings could greatly extend the lifetime of geothermal wells and make them more economically competitive and technically viable.
Publications
Thermomechanical Modeling of High-Temperature Bonded Interface Materials, Die-Attach Materials for High-Temperature Applications in Microelectronics Packaging, Springer Nature Link (2019)
Metal-Organic-Inorganic Nanocomposite Thermal Interface Materials With Ultralow Thermal Resistances, American Chemical Society Applied Materials and Interfaces (2017)
Reliability of Emerging Bonded Interface Materials for Large-Area Attachments, IEEE Transactions on Components, Packaging, and Manufacturing Technology (2016)
Contact
Share
Last Updated Feb. 7, 2025