Lightning No Match for Wind Turbine Blade Protection System
Research Opens Doors to Patent-Pending Thermal Welding Process
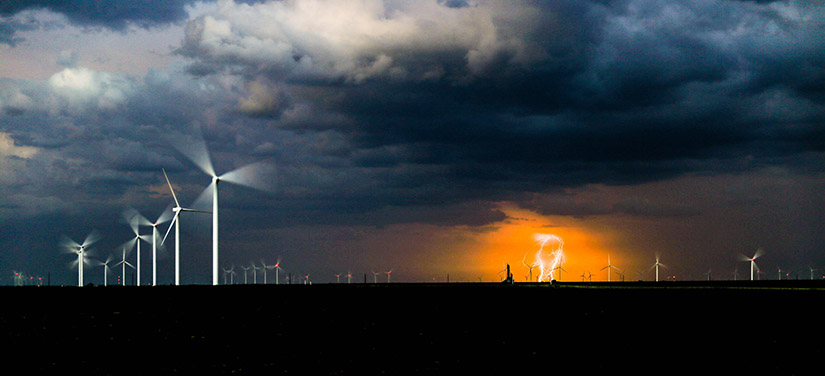
Standing hundreds of feet above ground, wind turbines—like tall trees, buildings, and telephone poles—are easy targets for lightning. Just by virtue of their height, they will get struck.
Lightning protection systems exist for conventional wind turbine blades. But protection was needed for blades made from a new type of material—thermoplastic resin composites—and manufactured using an innovative thermal (heat-based) welding process developed by scientists at the National Renewable Energy Laboratory (NREL).
Thermoplastic materials, like plastic bottles, can be more easily recycled than the thermoset materials commonly used to make wind turbine blades today. While thermoset materials need to be heated to cure, thermoplastics cure at room temperature, which reduces both blade manufacturing times and costs.
NREL’s patent-pending thermal welding process for thermoplastic blades allows for these benefits and even adds to them by replacing the adhesives currently used to bond blade components. The use of welding instead of adhesives eliminates the downsides of added weight and cracking potential.
While thermal welding offers benefits, it also requires adding within the blade a metal heating element—which can attract lightning. As a result, a team of NREL researchers led by Robynne Murray and supported by General Electric (GE) and LM Wind Power (a GE subsidiary) invented a new lightning protection system to keep the novel thermoplastic materials safe.
Thermal Welding Goes for the Patent
In 2018, Robynne Murray, an NREL engineer who specializes in advanced manufacturing methods and materials for wind turbine blades, received a two-year NREL Laboratory Directed Research and Development award to research thermal welding of thermoplastic wind turbine blades.
To make one of these new blades, a vacuum pulls liquid thermoplastic resin into the fiberglass material that is placed in a mold for each blade half. To weld the blade halves together, scientists sandwich a conductive material—such as an expanded metal foil or carbon fiber—between the two blade components and attach a wire to a power source. This creates the heating element. As current flows through this element, the thermoplastic materials melt. Once they are melted, the current is switched off and the bond cools under pressure.
Murray’s research demonstrated that thermal welding can effectively bond thermoplastic wind turbine blade segments. She submitted a patent application on the process in 2018.
A Pathway for Lightning
Thermal welding works. But it leaves the conductive heating element, which can attract lightning, within the blade.
“Thermal welding is an important step in the progression of commercializing thermoplastic materials for wind blades, but what happens when lightning strikes a thermal-welded blade? That was an unanswered question and a big concern,” Murray said. “For thermal welding of thermoplastic blades to become commercially viable, it is critical that the conductive bond lines be protected from a lightning strike.”
Partnering with GE and LM Wind Power, Murray submitted a research proposal to the U.S. Department of Energy’s (DOE's) Technology Commercialization Fund (TCF). TCF awards are designed to advance technology developed at national laboratories toward commercialization while encouraging lab-industry partnerships.
“With our partnership with GE, a company that can take the thermal welding process to commercialization, our TCF was a strong proposal,” Murray said. “Together, we wanted to determine whether we can protect these blades from lightning strikes and eliminate a big reason to stop us from using the technology.”
In 2019, the team received $150,000 in TCF funding; GE matched that amount.
The research partners set up shop in NREL’s Composites Manufacturing Education and Technology (CoMET) Facility to demonstrate that thermoplastic blades sealed using thermal welding can be protected from lightning strikes.
The team infused an expanded aluminum foil into the blade skin to divert lightning current away from the metal heating elements. They then completed experiments using a simulation that showed that a lightning strike would not cause blade failure with the lightning protection system in place.
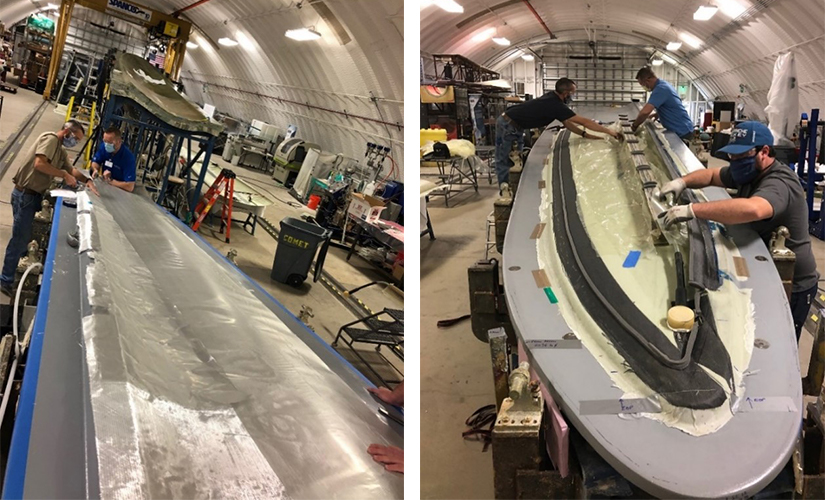
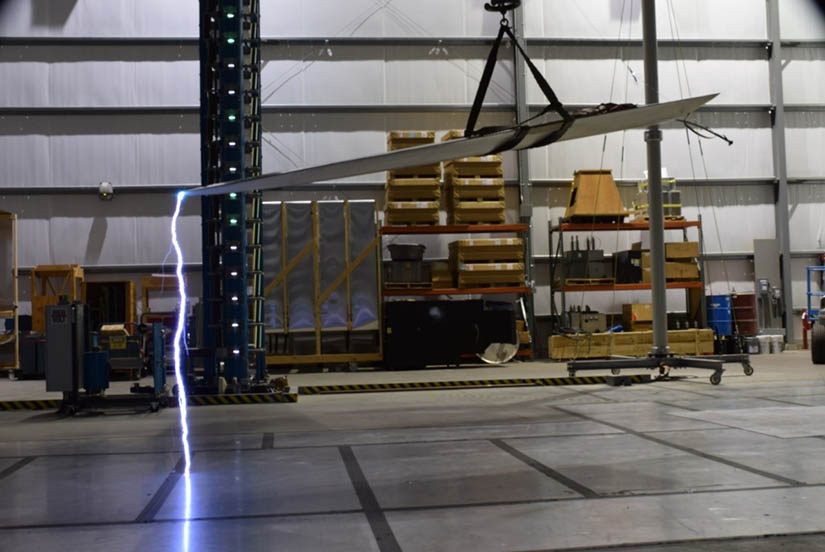
Physical damage tests—which subject the blades to high currents of electricity—demonstrated that about 80% of the electric current went into the expanded aluminum foil layer for lightning protection and not into the blade skin. The carbon fiber beneath the damaged area of the tip was also unscathed.
The research confirmed the design can protect wind turbine blades against failure caused by lightning strikes.
“LM Wind Power and GE Research were excited to work with NREL on the development of this technology and appreciated the support by DOE’s Technology Commercialization Fund. Thermal welding technology for thermoplastic, recyclable wind blades offers a significant opportunity to impact the sustainability and carbon footprint of wind blade structures,” said James Martin, director of blade platform deployment for LM Wind Power. “NREL’s focus on mitigating the lightning damage risks associated with the electrically conductive elements in the welded bond is a key challenge to be overcome, and their work has helped mature the technology toward potential commercialization.”
Still More Questions To Answer
The project has already delivered two strikes against lightning. Murray’s work developing a market-ready thermal welding system, however, is still at bat.
“We answered the question about lightning. But there are more questions to answer and more work to be done,” Murray said. “The next step for us is to do structural validation of thermally welded blade bond lines and blade tip segments. I hope we can do this in the next year or so.”
Read more about this project in Wind Engineering.